Challenges of Electrical Panels in India’s Climate
Operating in High Temperatures
India’s ambient temperatures range between 35°C to 50°C, creating a challenging environment for electrical panels and switchgear. Initially, equipment functions well, but prolonged exposure to heat accelerates aging and leads to:
- Overheating of connections.
- Damage to components.
- Insulation degradation.
- Increased risk of fire and arc flash incidents.
Temperature Limits for Electrical Safety
According to IEC standards and India’s weather conditions:
- Maximum allowable temperature for copper bus bars: ~140°C.
- Maximum for individual components: ~125°C.
- Maximum for externally insulated conductors: ~105°C.
Ensuring panels stay within these temperature limits is critical to maintaining safety and functionality.
Traditional Temperature Monitoring Techniques: Limitations
IR Thermography
One commonly used method for detecting overheating is high-resolution infrared (IR) thermography, which allows non-contact temperature measurements. However, it has limitations:
- Periodic Monitoring: Only provides snapshots of the panel’s condition during inspections.
- Missed Abnormalities: Issues between inspection intervals remain undetected.
- Access Challenges: Hidden areas or panels that cannot be opened during operation are difficult to inspect.
The Next Generation Solution: Hot Spot Monitors
Continuous Temperature Monitoring
Hot Spot Monitors offer a robust solution for continuous temperature monitoring of electrical panels. They are ideal for detecting hotspots and temperature abnormalities in:
- Bus bars.
- MCCs (Motor Control Centers).
- Drive panels.
- Switchgear and bus ducts.
Advanced Technology
Key features of Hot Spot Monitors include:
- Non-Conductive Fiber Optic Technology: Safe and simple to install in low, medium, and high-voltage systems (up to 80kV).
- IoT-Enabled Functionality: Logs temperature data, generates alarms, and trends variations to identify potential faults.
- Real-Time Insights: Offers immediate feedback on equipment health and alerts for abnormal temperatures.
- Seamless Integration: Can be easily integrated with existing control systems.
Advantages of IoT-Enabled Hot Spot Monitors
- Improved Safety: Prevents accidents by providing early warnings of overheating.
- Predictive Maintenance: Allows maintenance teams to proactively schedule repairs, reducing unplanned downtime.
- Enhanced Productivity: Supports a safe and efficient work environment, ensuring maximum equipment uptime and reliability.
Creating a Safer and More Productive Work Environment
Pima Controls Pvt. Ltd.: Your Partner in Industrial Safety and Efficiency
Pima Controls Pvt. Ltd., an ISO 9001:2015 certified company, has been a trusted provider of industrial automation and electrical solutions since 1986. Their expertise includes:
- Distribution of World-Class Products: Partnering with leading global brands.
- Predictive Maintenance Strategies: Helping machine builders and end-users enhance operational efficiency and safety.
Subscribe for More Insights

How APFC Panels Save You Lakhs in Electricity Bills
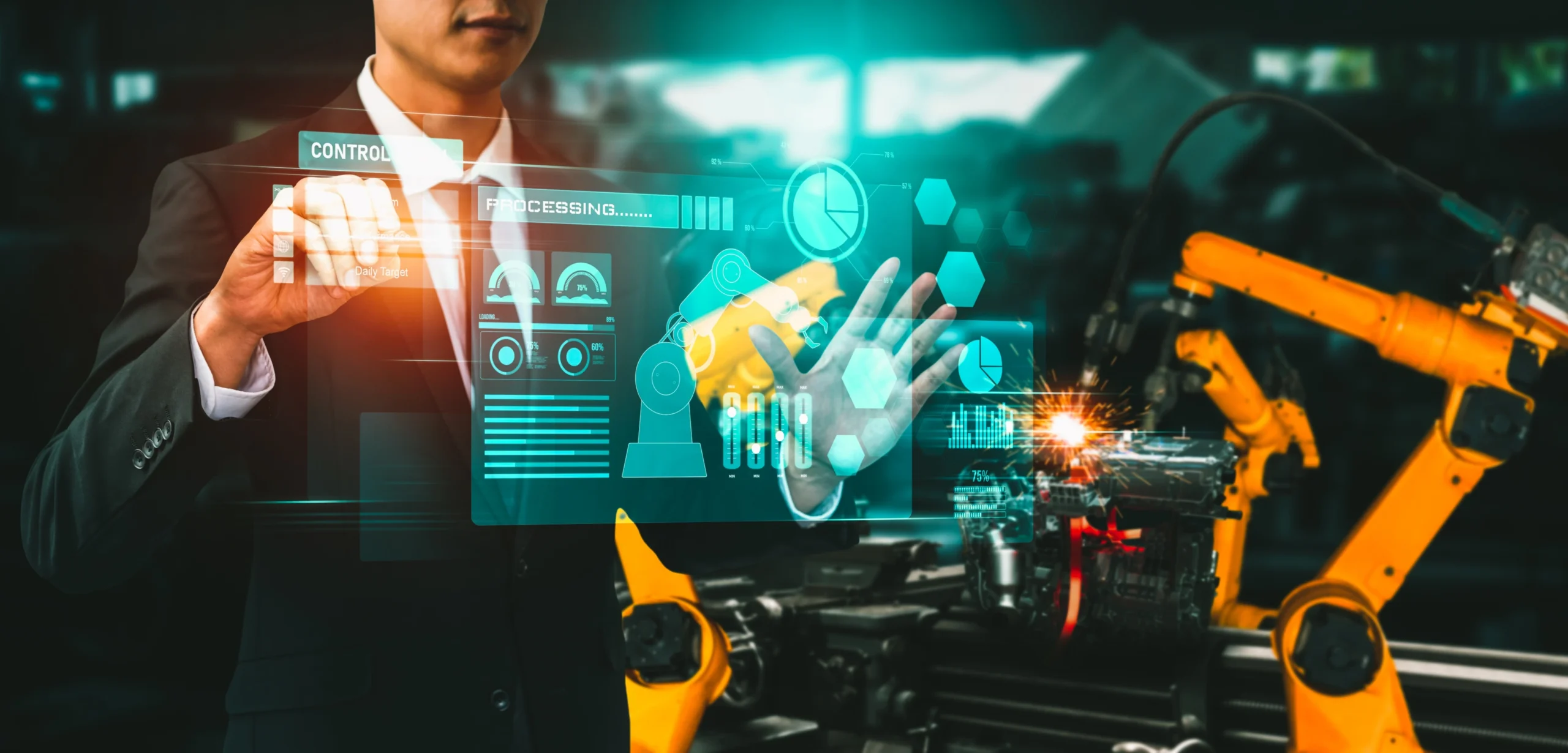
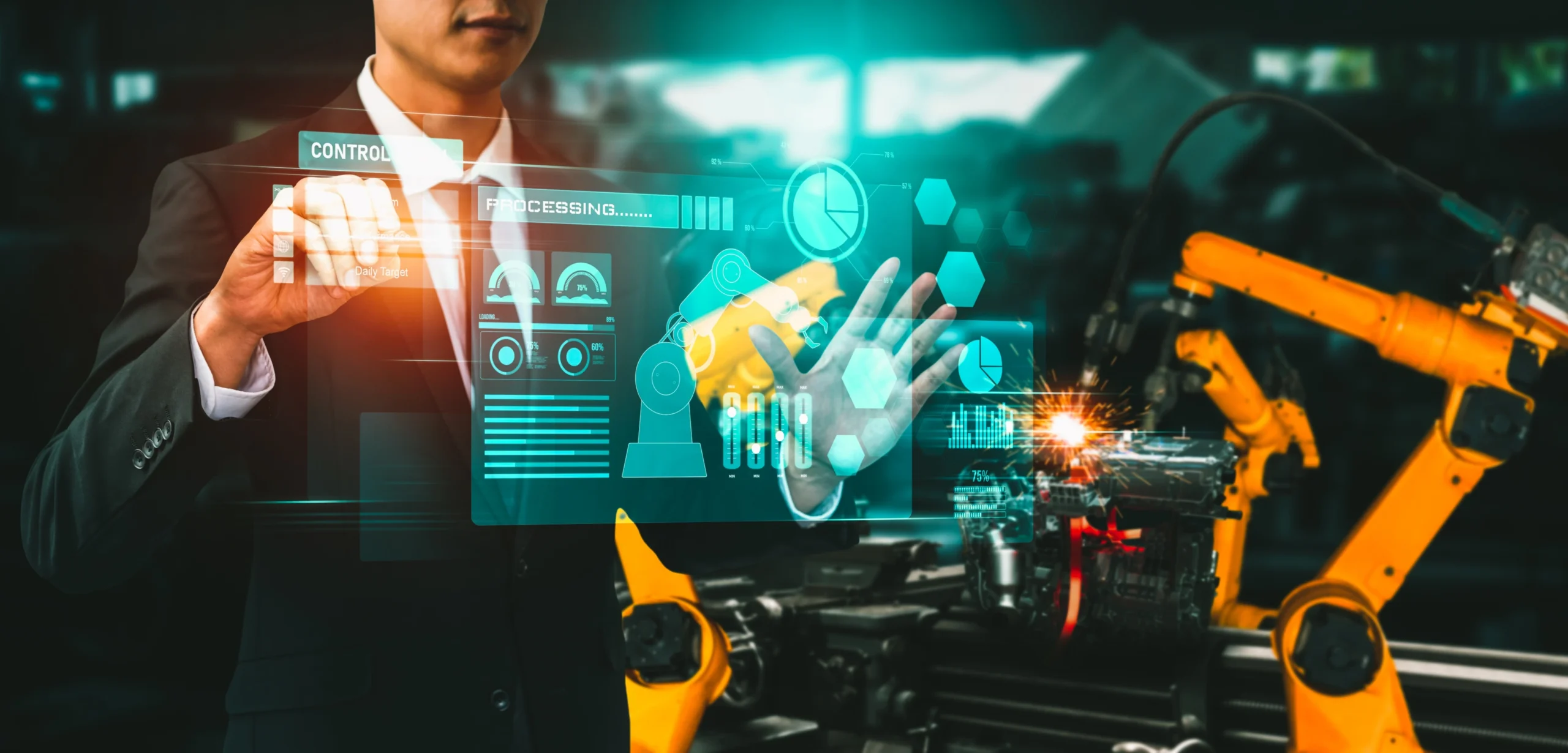
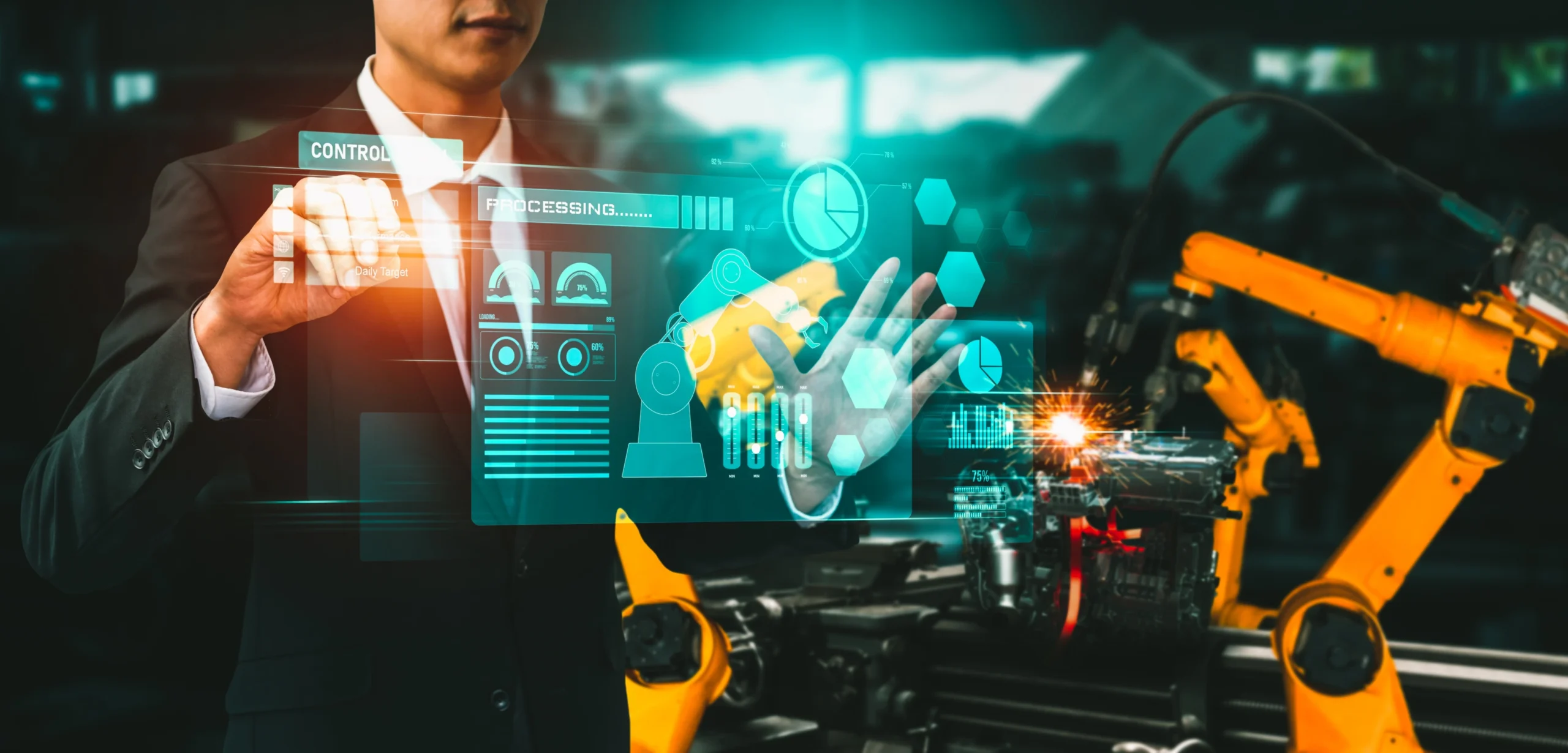
Is It Time to Upgrade Your UPS System? Signs Your Battery Needs Replacement
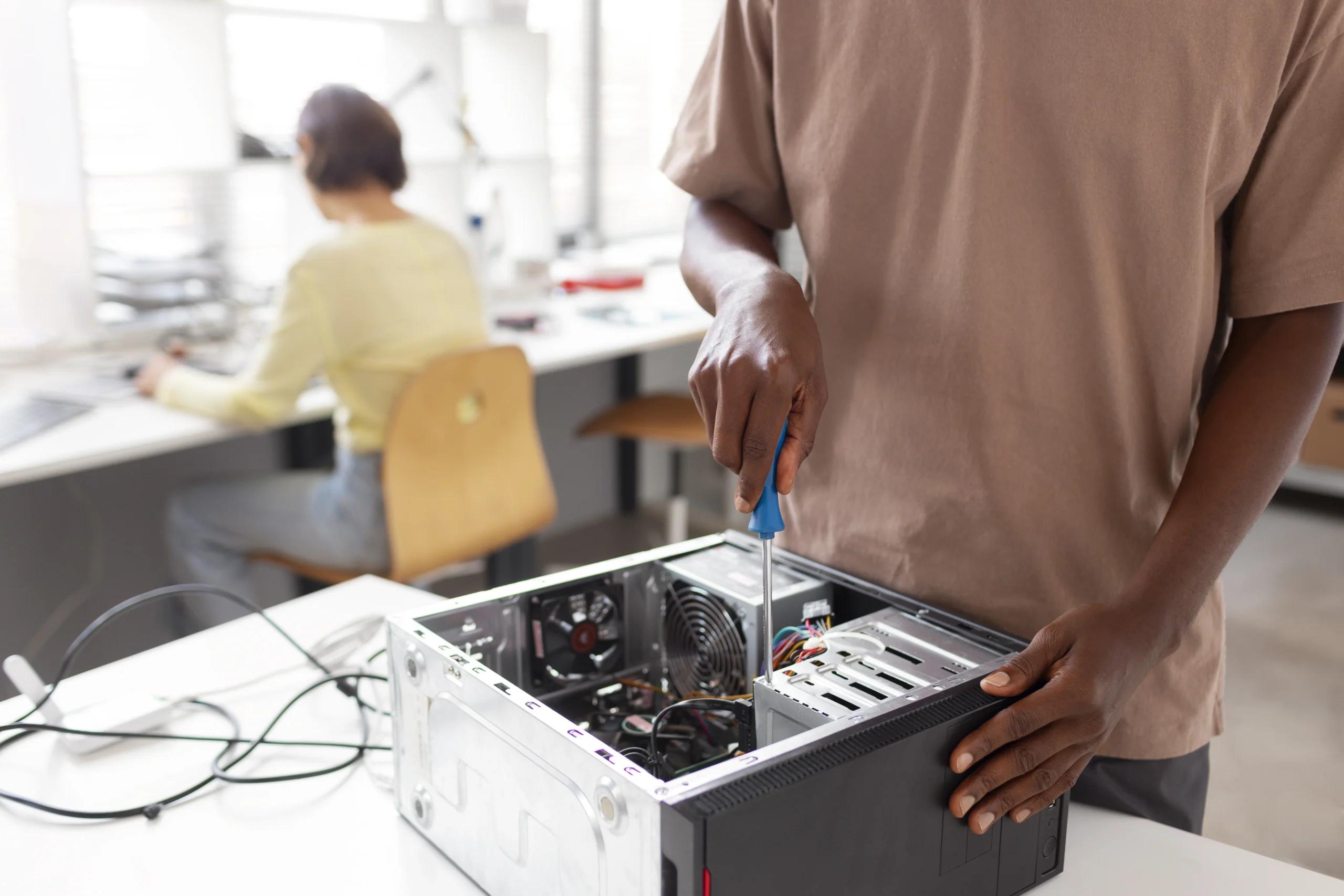
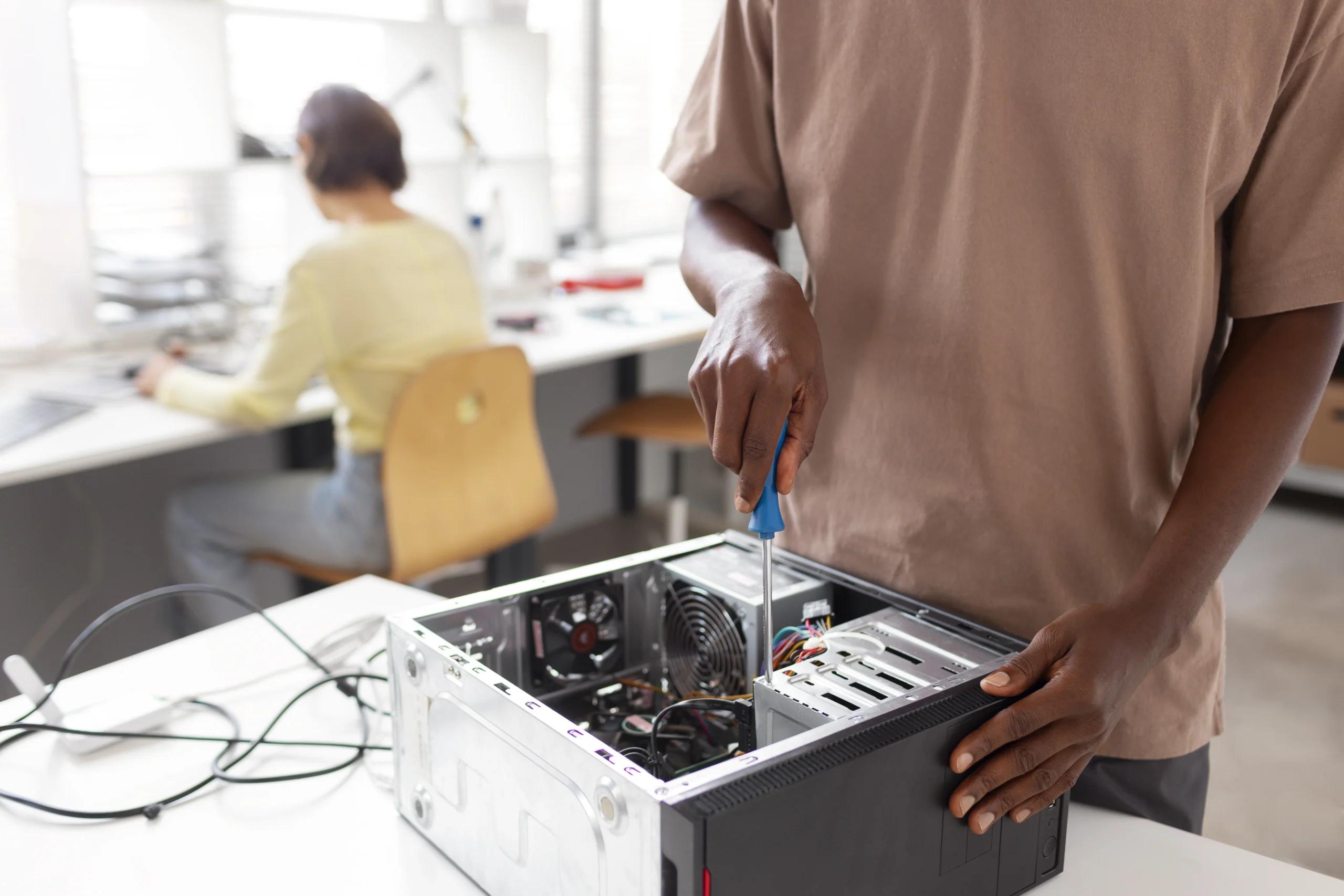
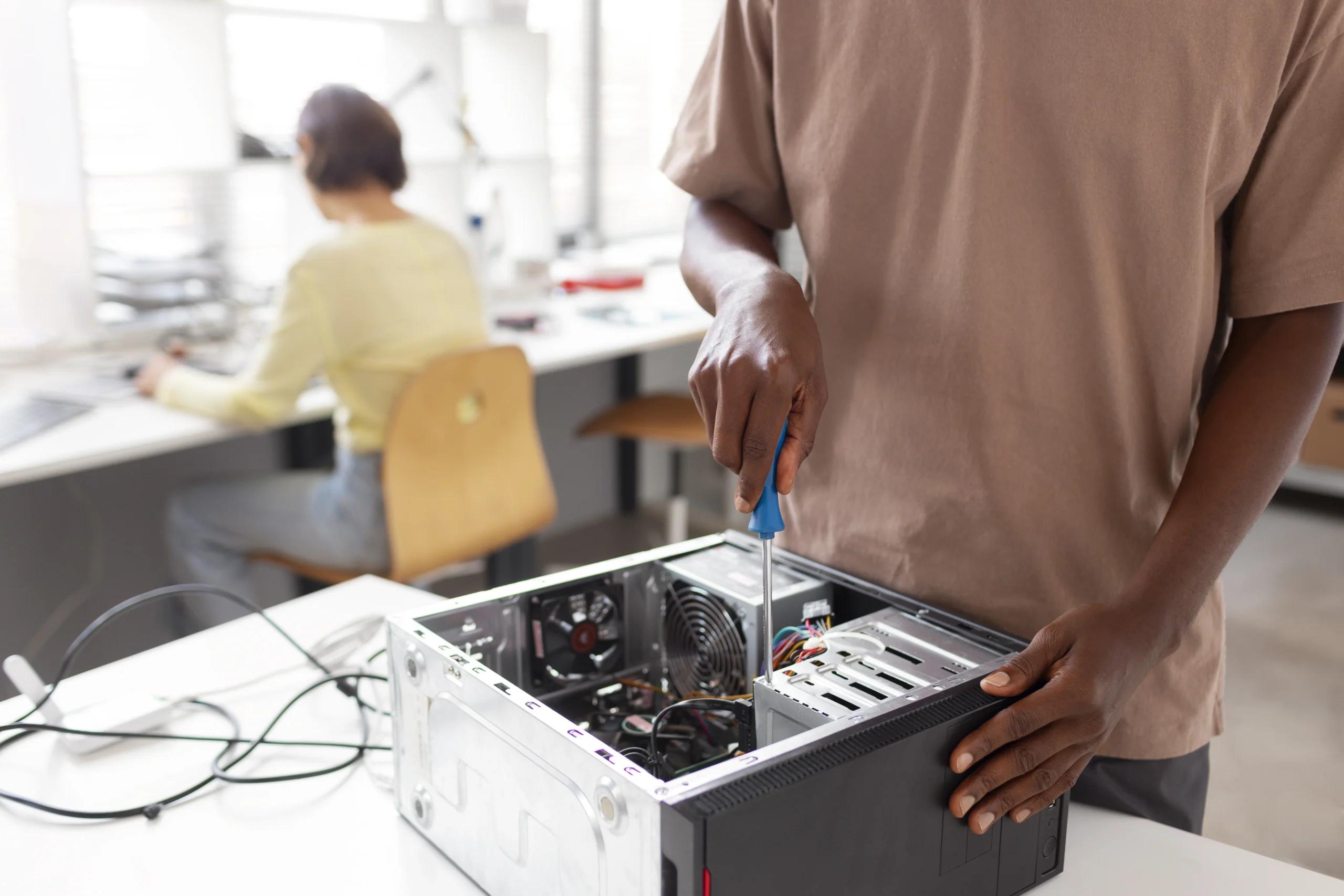
How to Calculate UPS Capacity for Your Business Needs
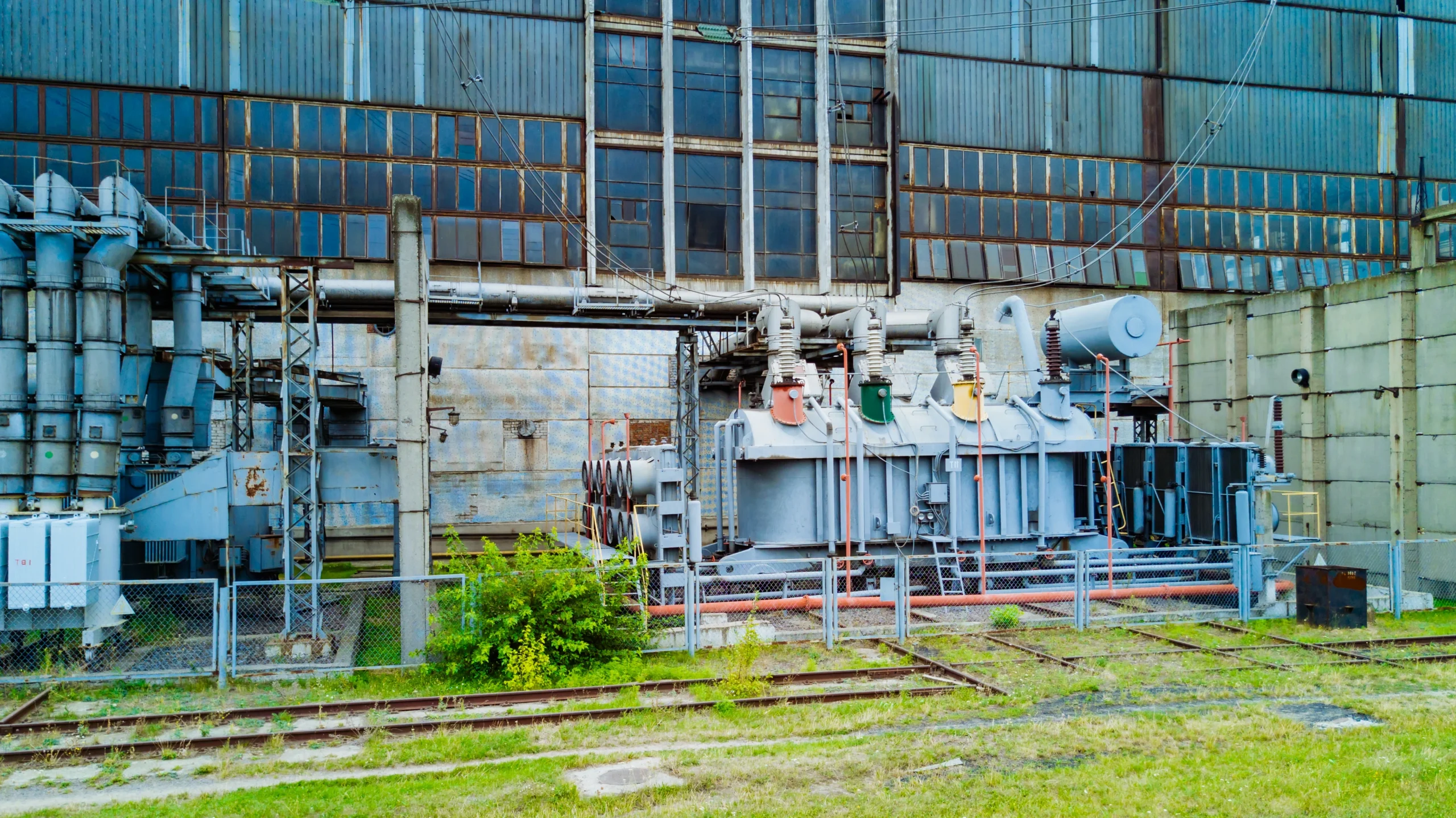
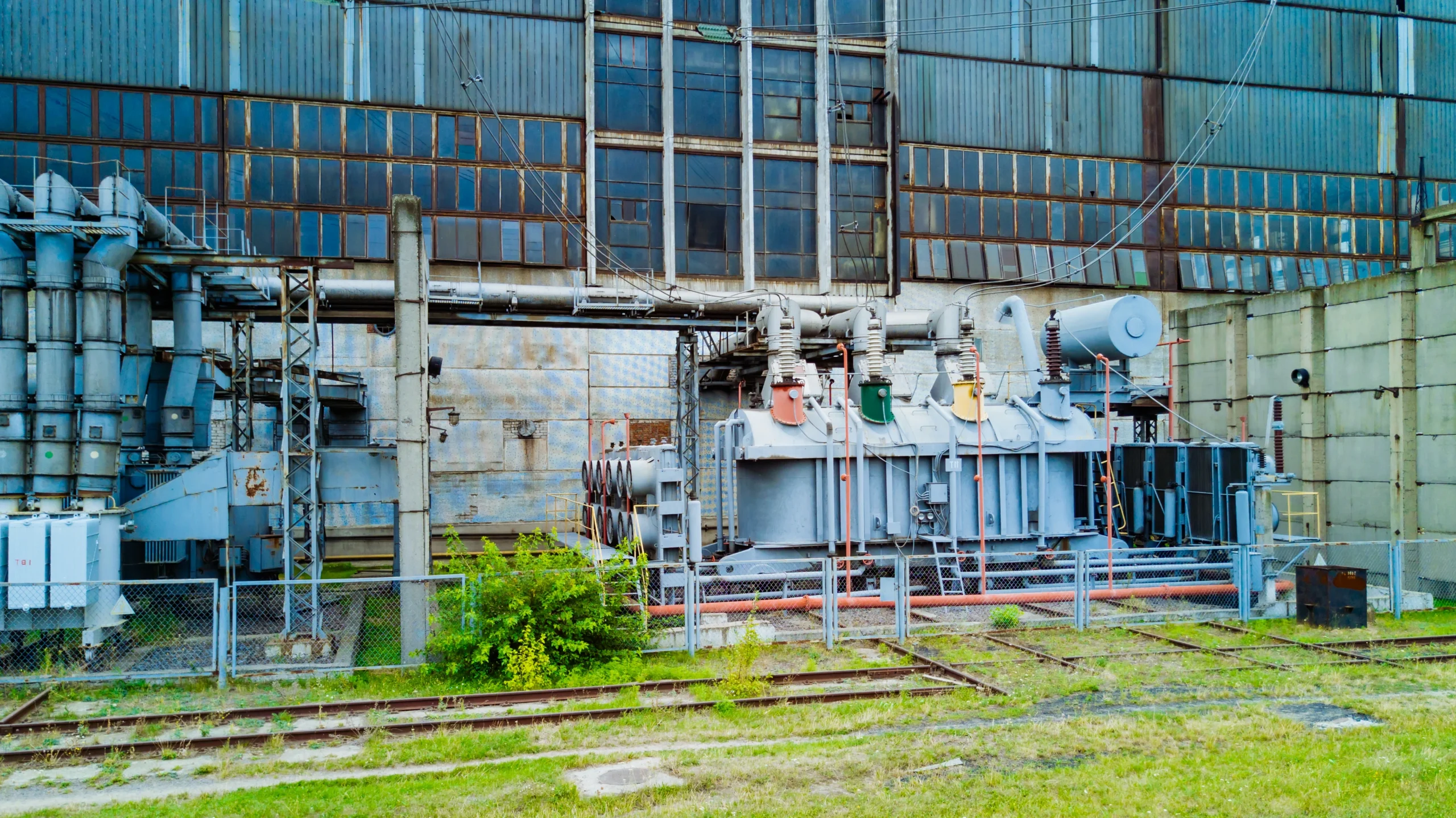
Top Electrical Panel Manufacturer in Gujarat: Find the Best Electrical Panel Suppliers
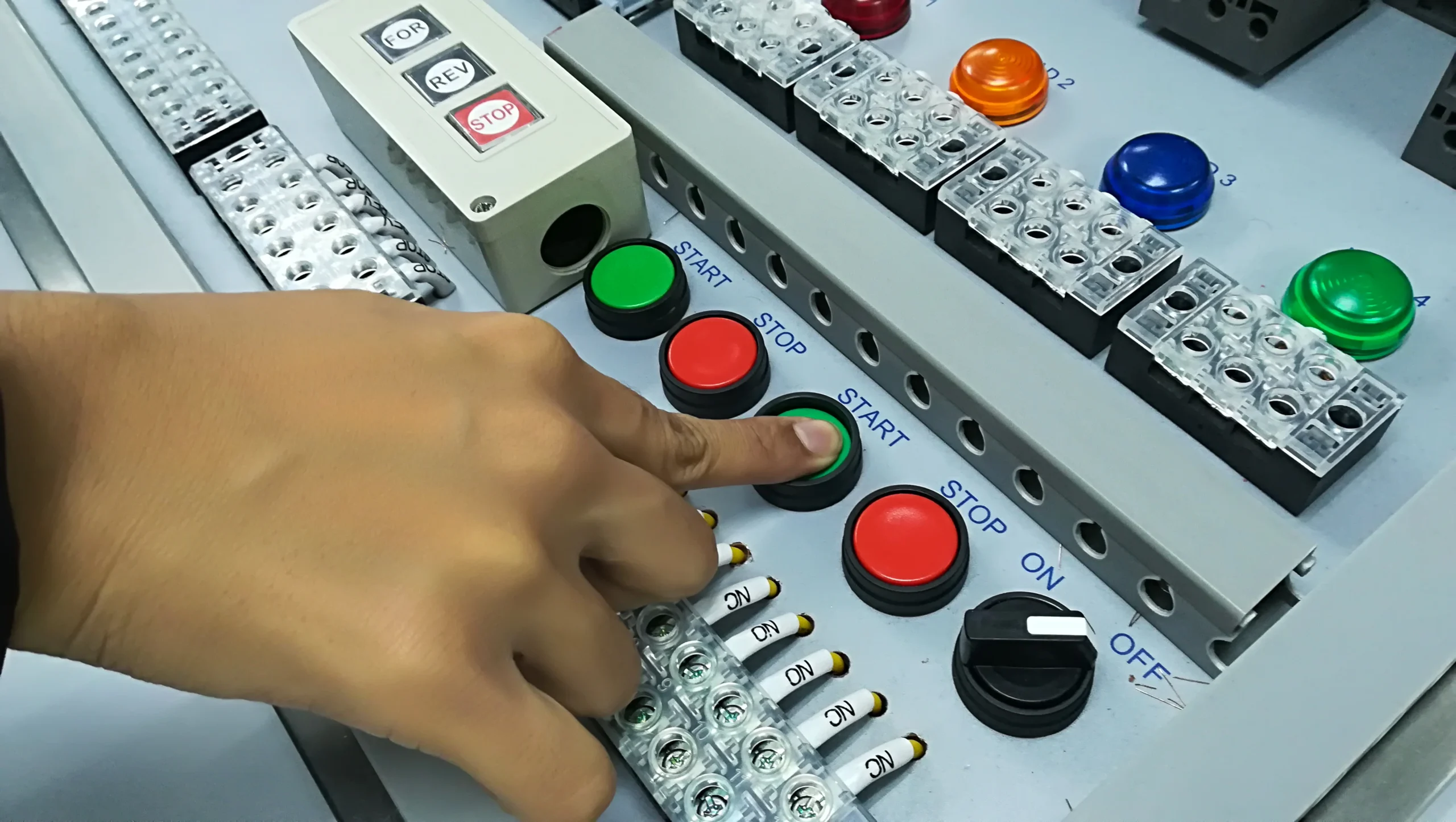
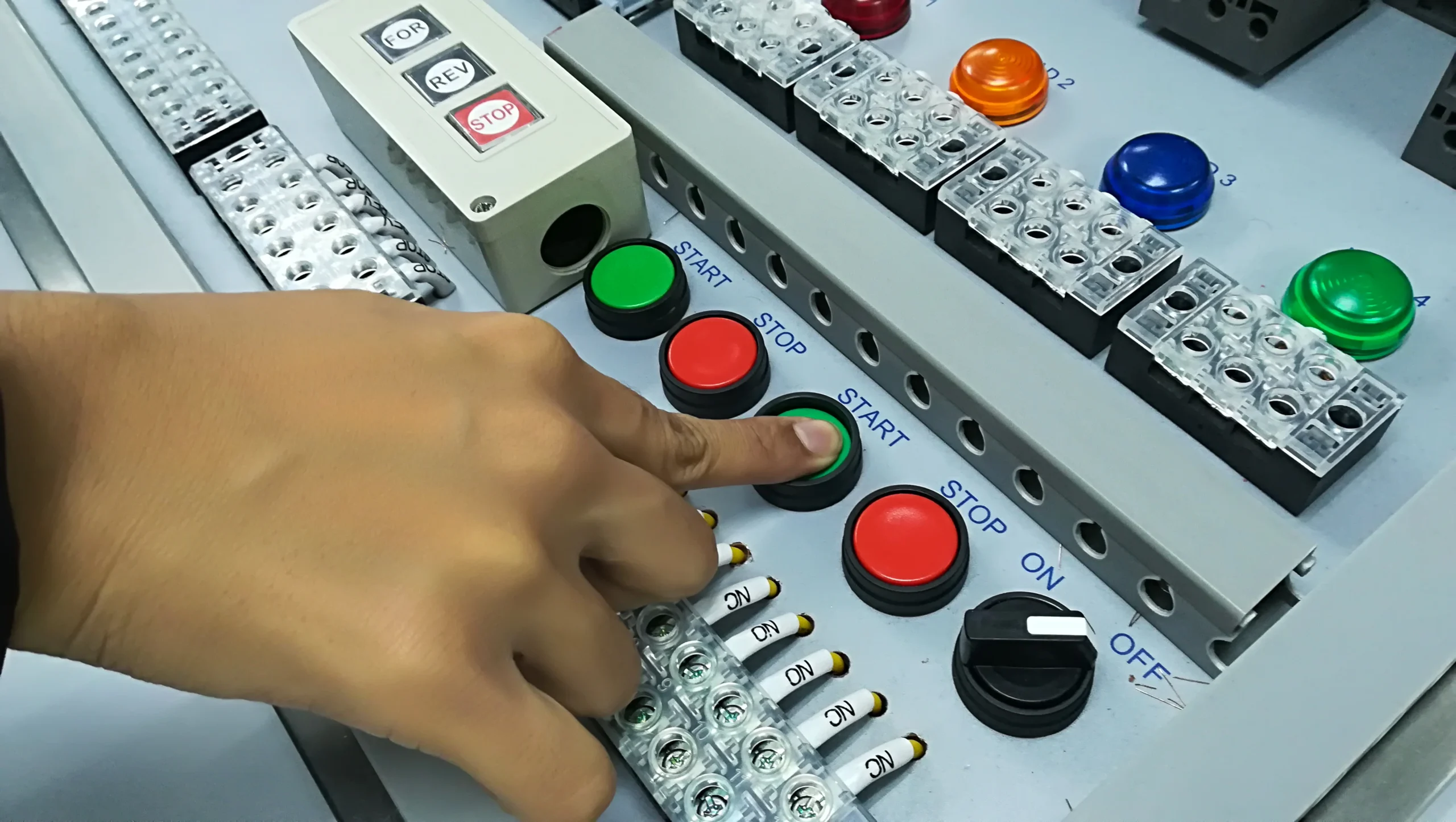
How to Choose the Best UL 508A Control Panels for Industrial Use in USA
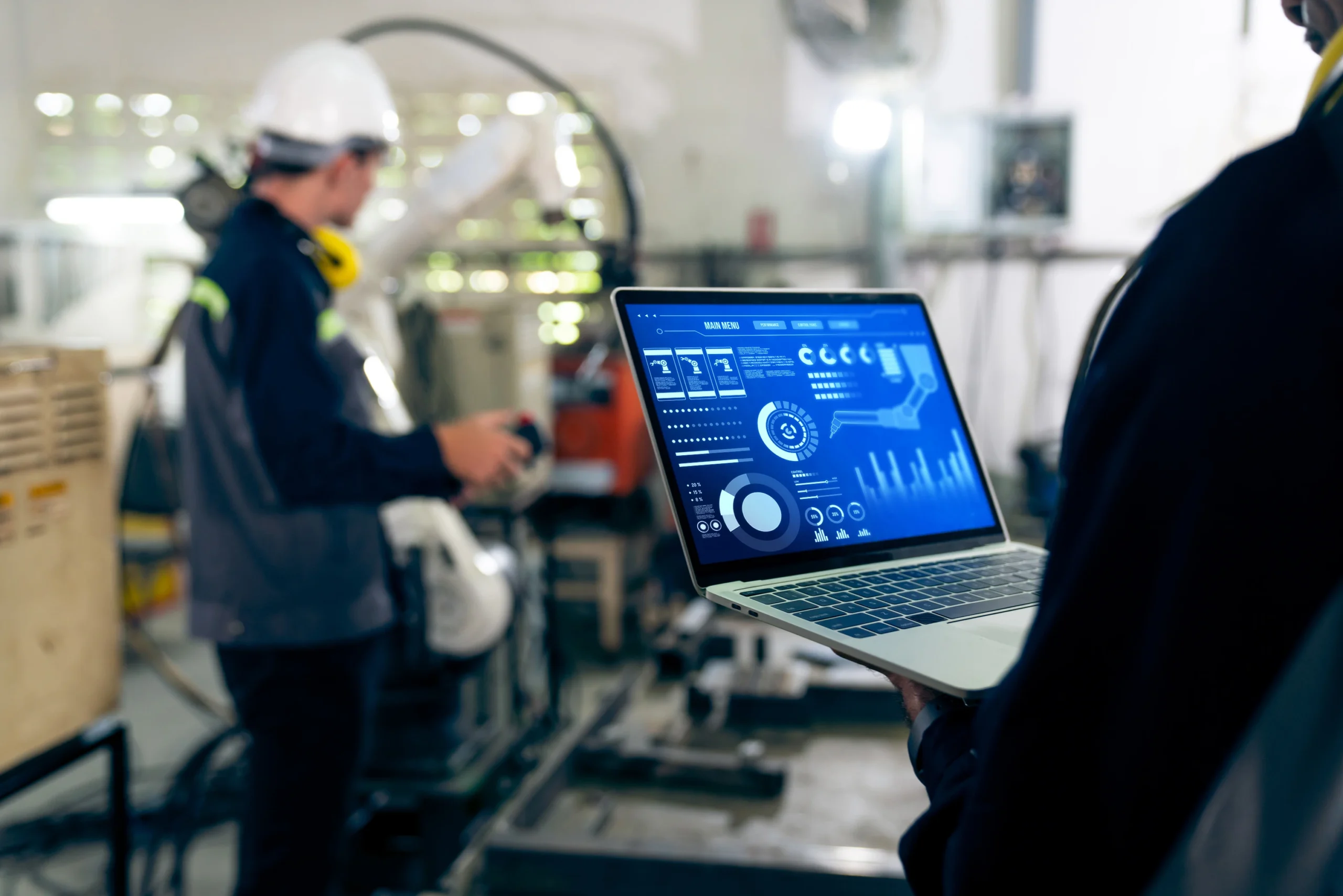
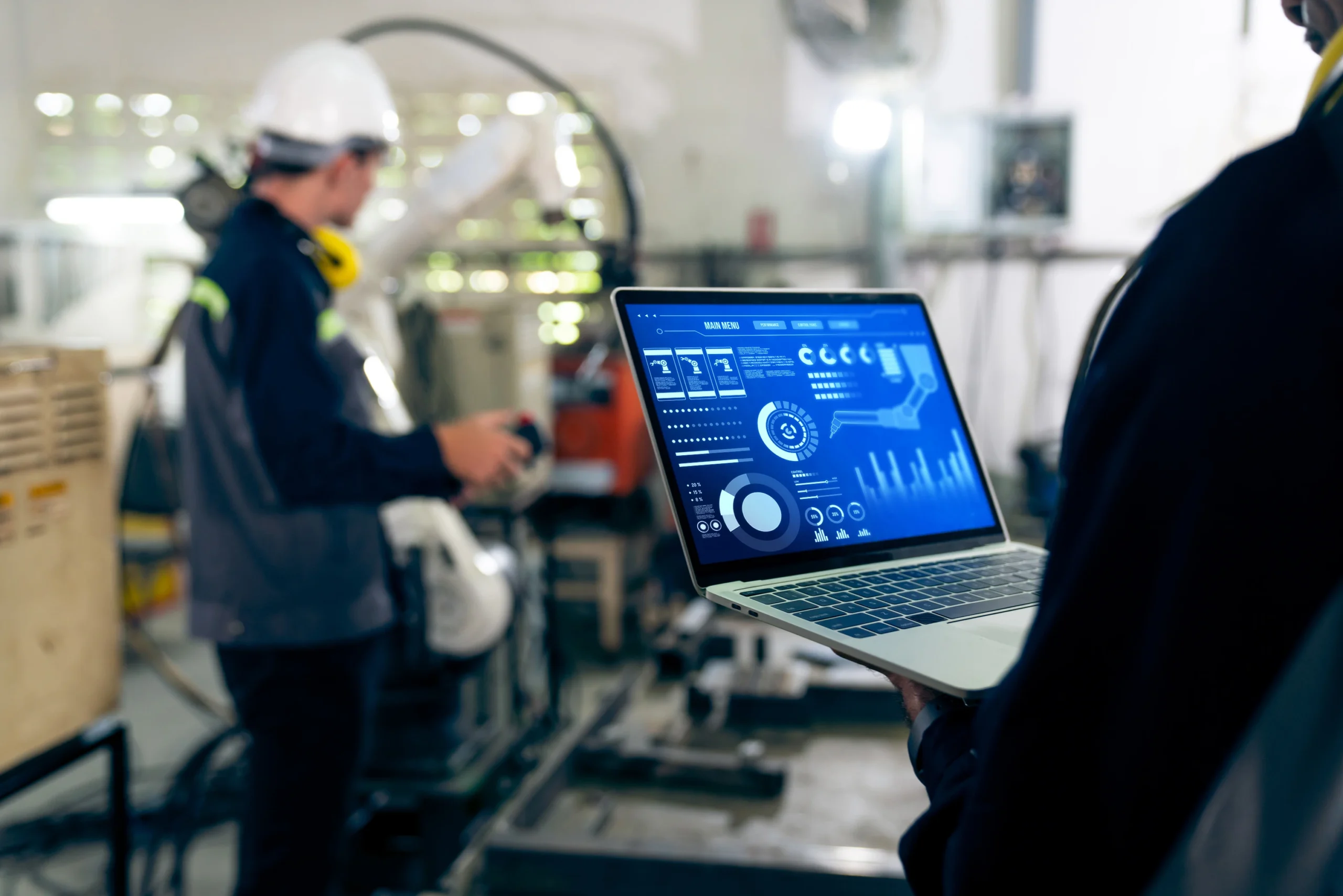
Role of UPS Systems in Automation: Minimizing Downtime and Boosting Productivity

How APFC Panels Save You Lakhs in Electricity Bills
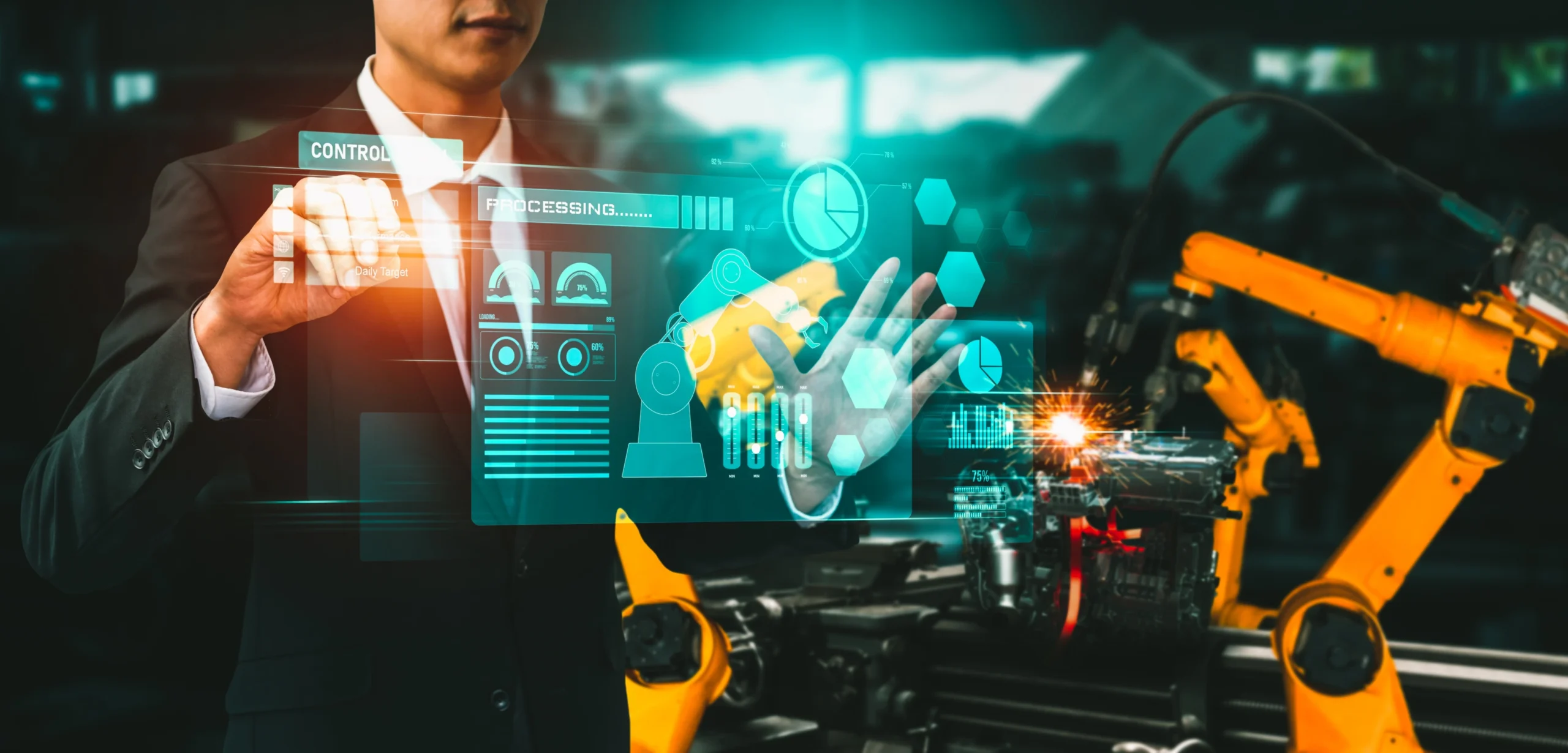
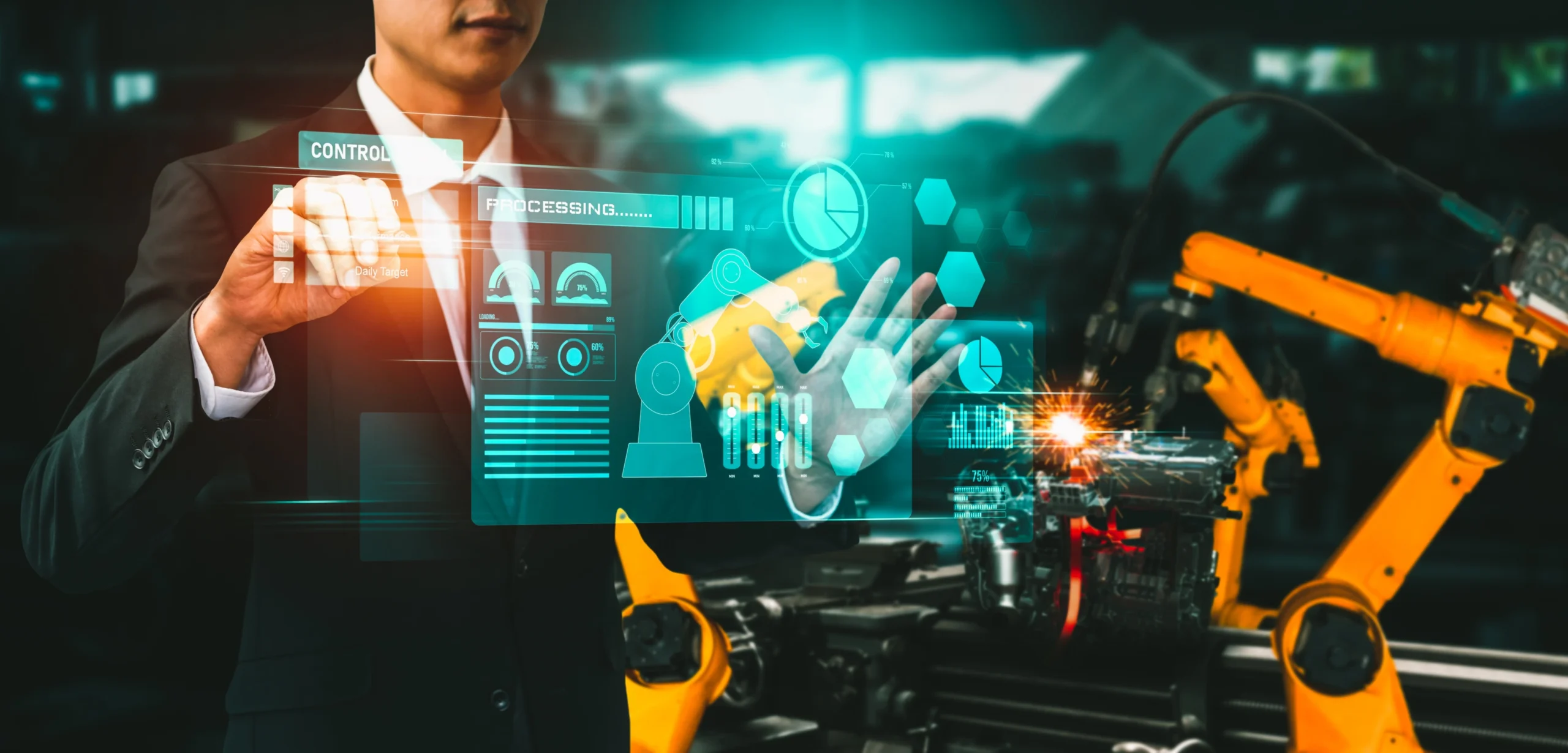
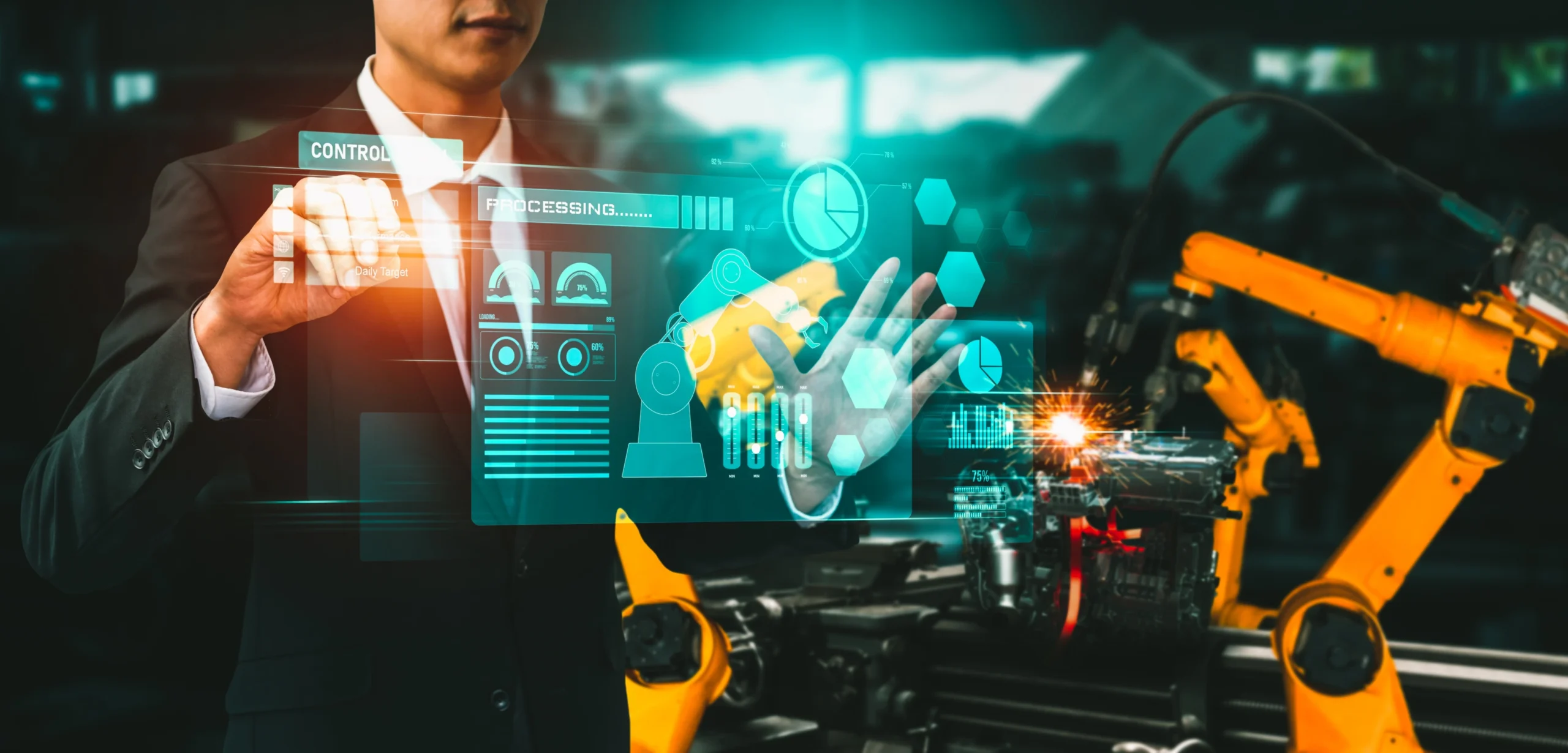
Is It Time to Upgrade Your UPS System? Signs Your Battery Needs Replacement
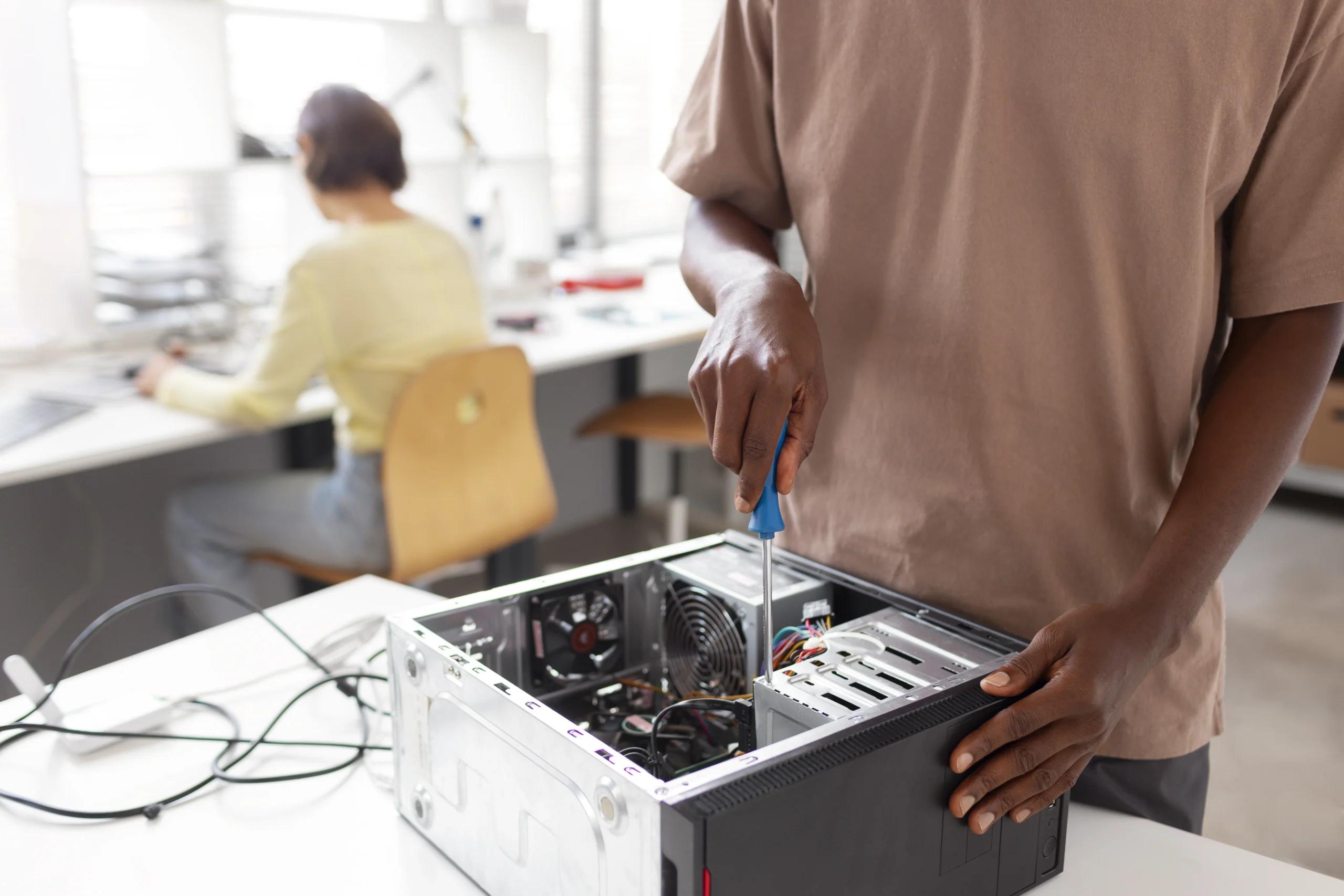
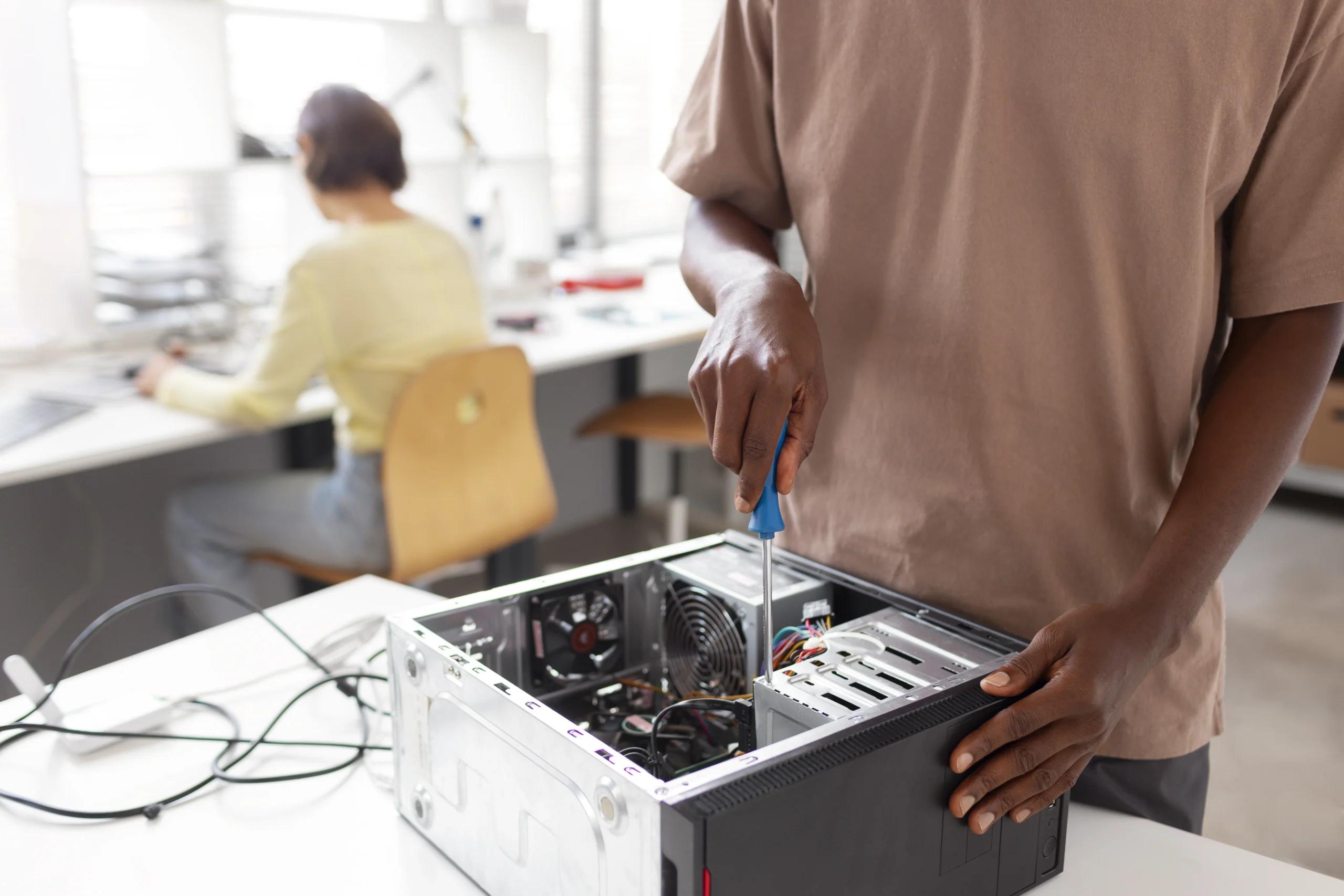
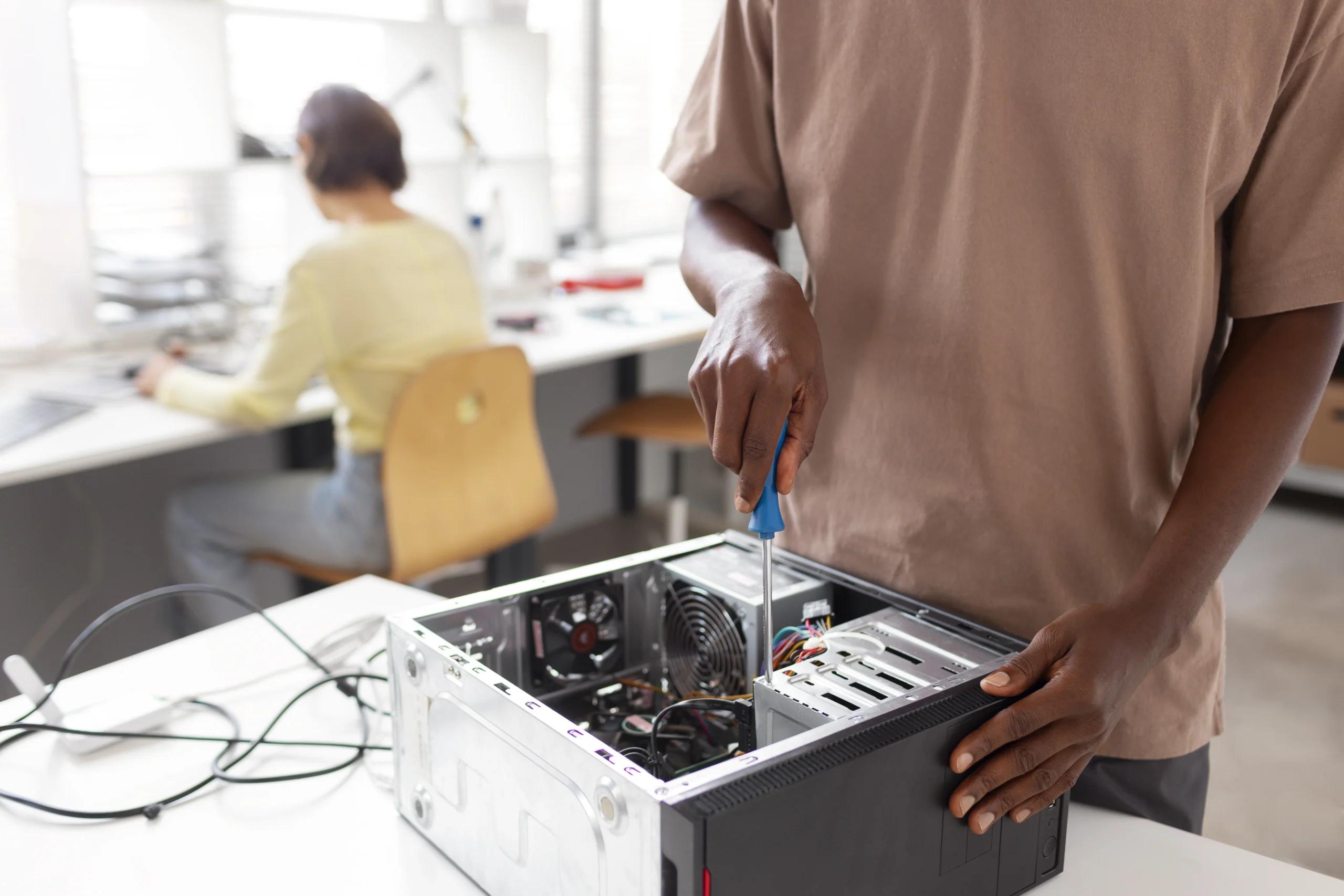