Predictive maintenance (PdM) has long been a fascinating area for industries. However, understanding it or providing insights into its application requires domain expertise. Today, a significant shift in operational and maintenance strategies is evident across industries.
Drivers for Change: The Need for PdM Tools
Increased Productivity Demands
Industries are under pressure to achieve higher operational efficiency.
Uptime Expectations
Equipment downtime can lead to significant losses, necessitating predictive solutions.
Skilled Labor Shortages
A decline in the availability of qualified maintenance personnel has pushed industries to rely on advanced technologies.
From Manual Inspections to Advanced PdM Tools
Traditional Maintenance Practices
In the past, skilled professionals relied on their senses—listening to equipment noises or feeling vibrations—to detect issues. This approach, while effective in some cases, is:
- Unscalable: Limited to individual expertise.
- Error-Prone: Subject to human limitations.
The Evolution of Predictive Maintenance
Modern techniques leverage advanced tools such as vibration sensors. Here’s how they work:
- Mounted Probes: Capture equipment vibrations and send signals for analysis.
- Signal Analysis: Similar to an ECG, professionals interpret the signal patterns to identify potential failures.
While effective, these solutions come with challenges:
- High cost of skilled professionals and equipment.
- Complex installation involving extensive wiring.
The Wireless Revolution in PdM
Today’s wireless technologies have revolutionized predictive maintenance:
- Wireless Sensors: Mounted on equipment to transmit signals over long distances, eliminating the need for extensive wiring.
- Smart Software Integration: Logs data, provides insights, and enables AI-based analytics for predictive insights.
- Ease of Access: Delivers real-time updates on mobile devices, improving responsiveness and reducing downtime risks.
The Role of IoT, AI, and Cloud in PdM
Modern PdM integrates:
- IoT: Facilitates seamless connectivity between equipment and analytics platforms.
- AI: Analyzes vast data sets to predict issues with high accuracy.
- Cloud Computing: Provides accessibility and scalability, ensuring maintenance teams have insights at their fingertips.
Enhancing Operational Efficiency with PdM
Achieving Maximum OEE
Manufacturers strive to achieve optimal Overall Equipment Effectiveness (OEE), and predictive maintenance is a critical enabler.
The Advantages of Early Adoption
Industries adopting advanced PdM technologies reap benefits such as:
- Reduced downtime.
- Lower maintenance costs.
- Improved asset longevity.
Pima Controls Pvt. Ltd.: A Leader in Predictive Maintenance Solutions
Pima Controls Pvt. Ltd., an ISO 9001:2015 certified company, has been at the forefront of industrial automation and electrical solutions since 1986. Their expertise includes:
- Partnering with Global Leaders: Delivering high-quality products and services.
- Supporting Predictive Maintenance Strategies: Assisting machine builders and end-users in adopting cutting-edge PdM tools.
Subscribe for More Insights
Be a part of our ever growing community.
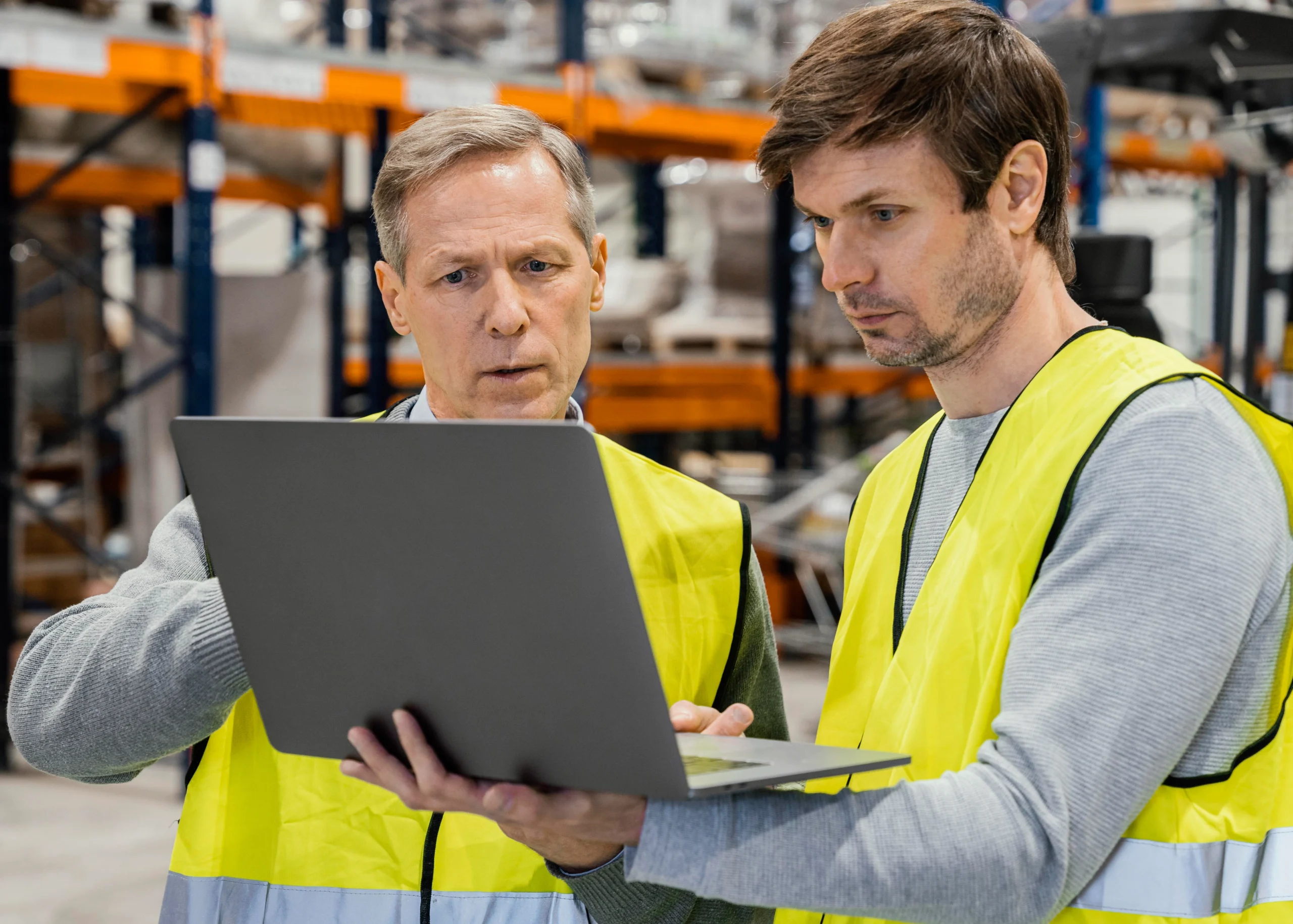
Smart Alerts in IIoT: Proactive Maintenance for Seamless Operations
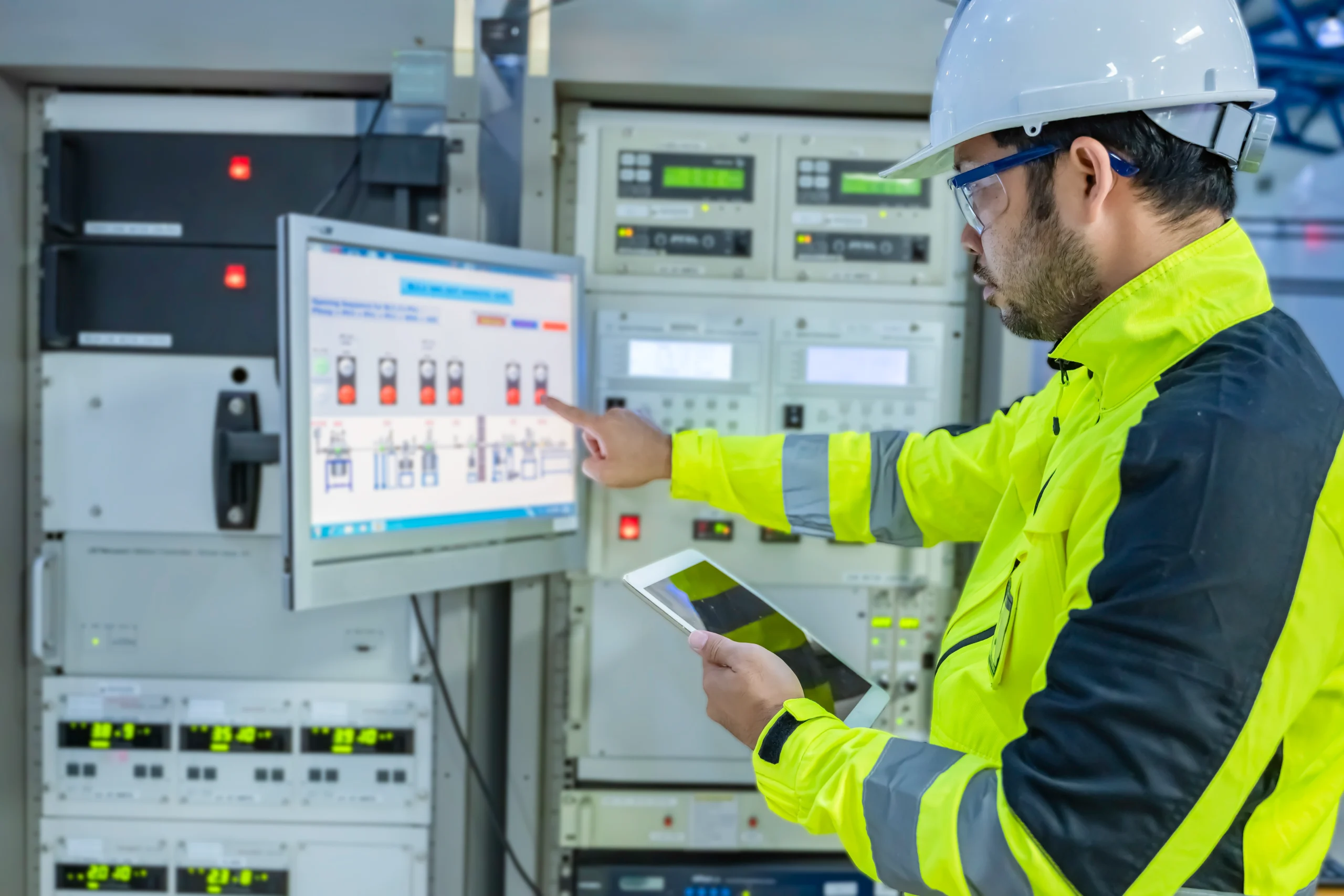
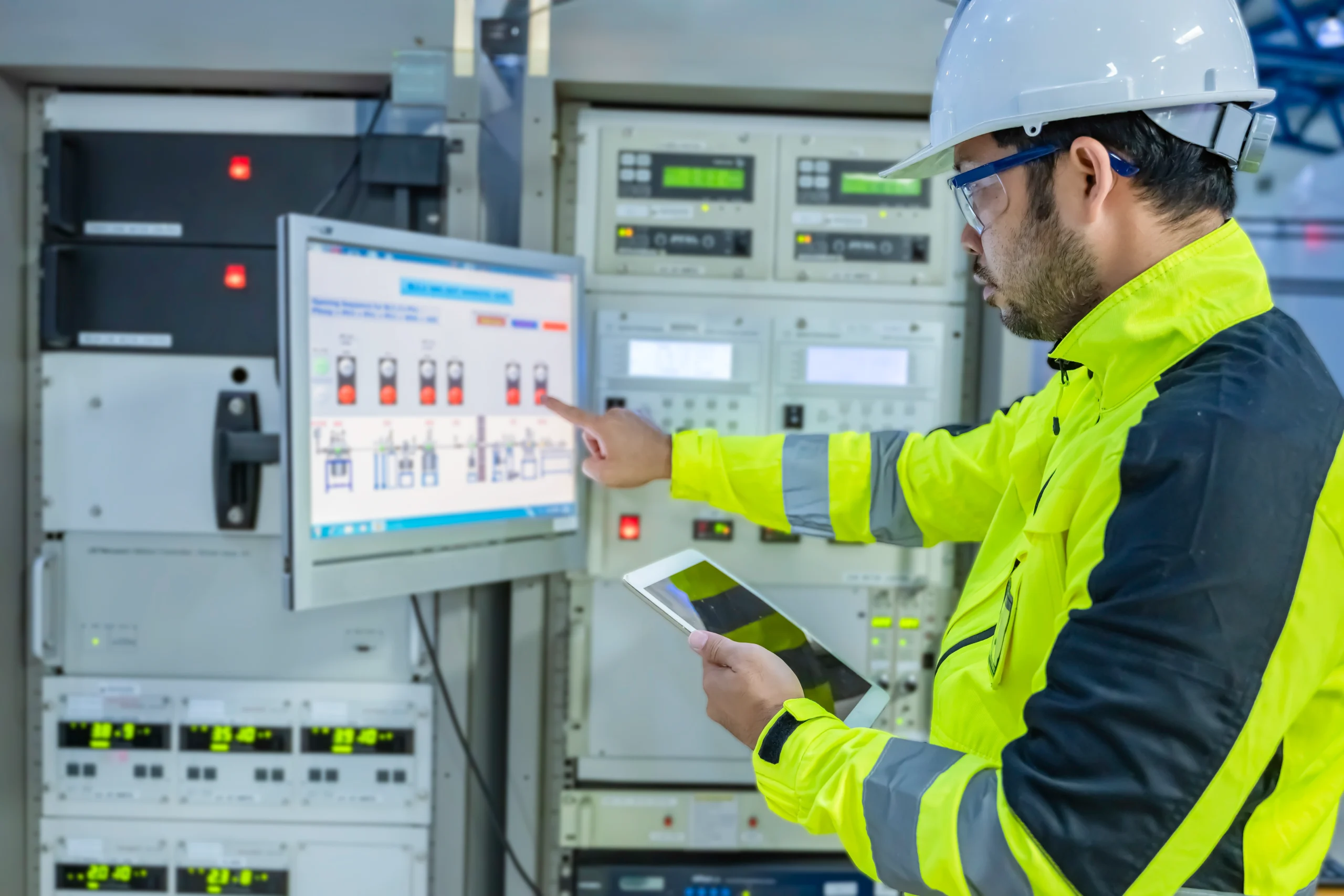
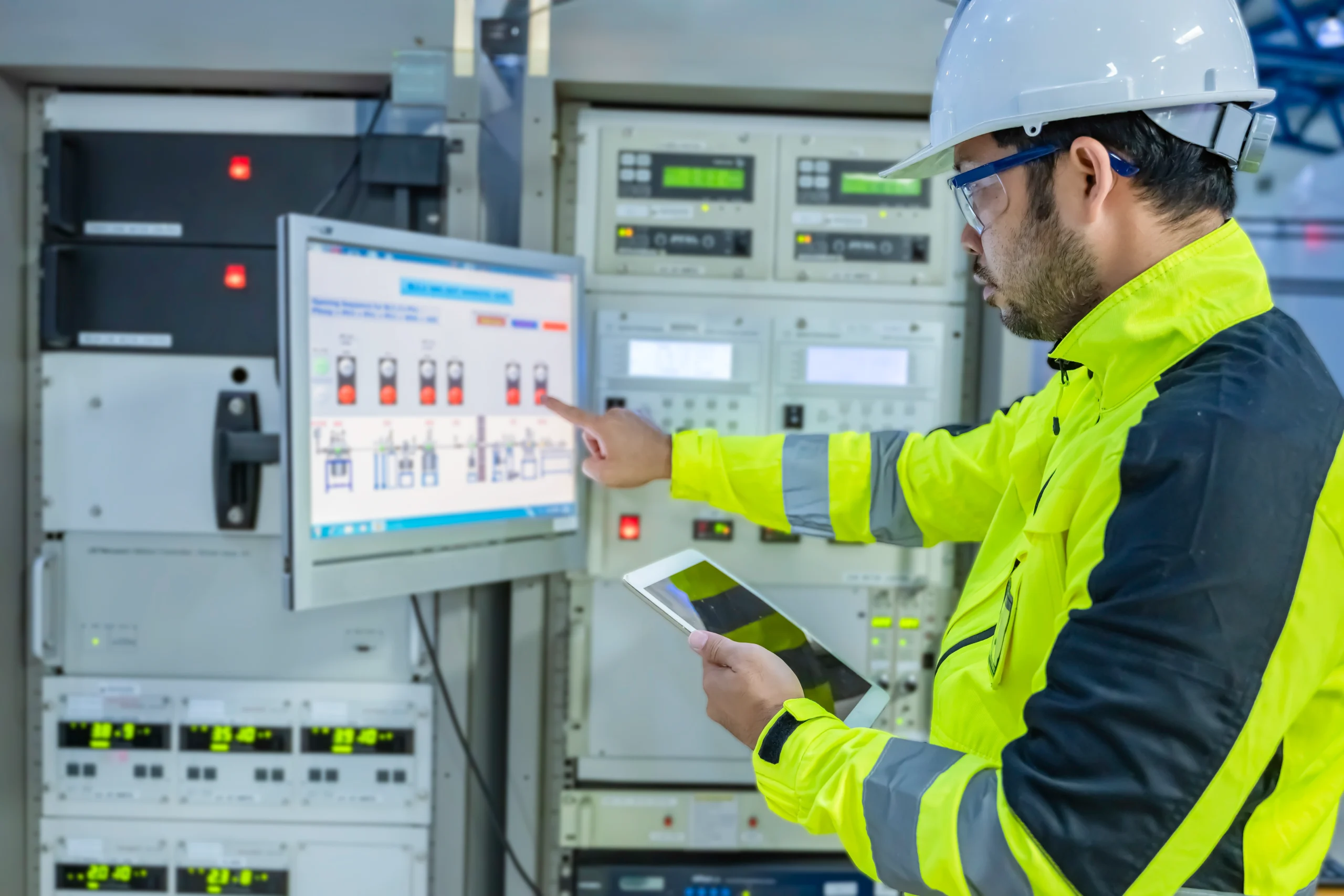
Energy Efficiency in Manufacturing: Leveraging IIoT for Cost Savings
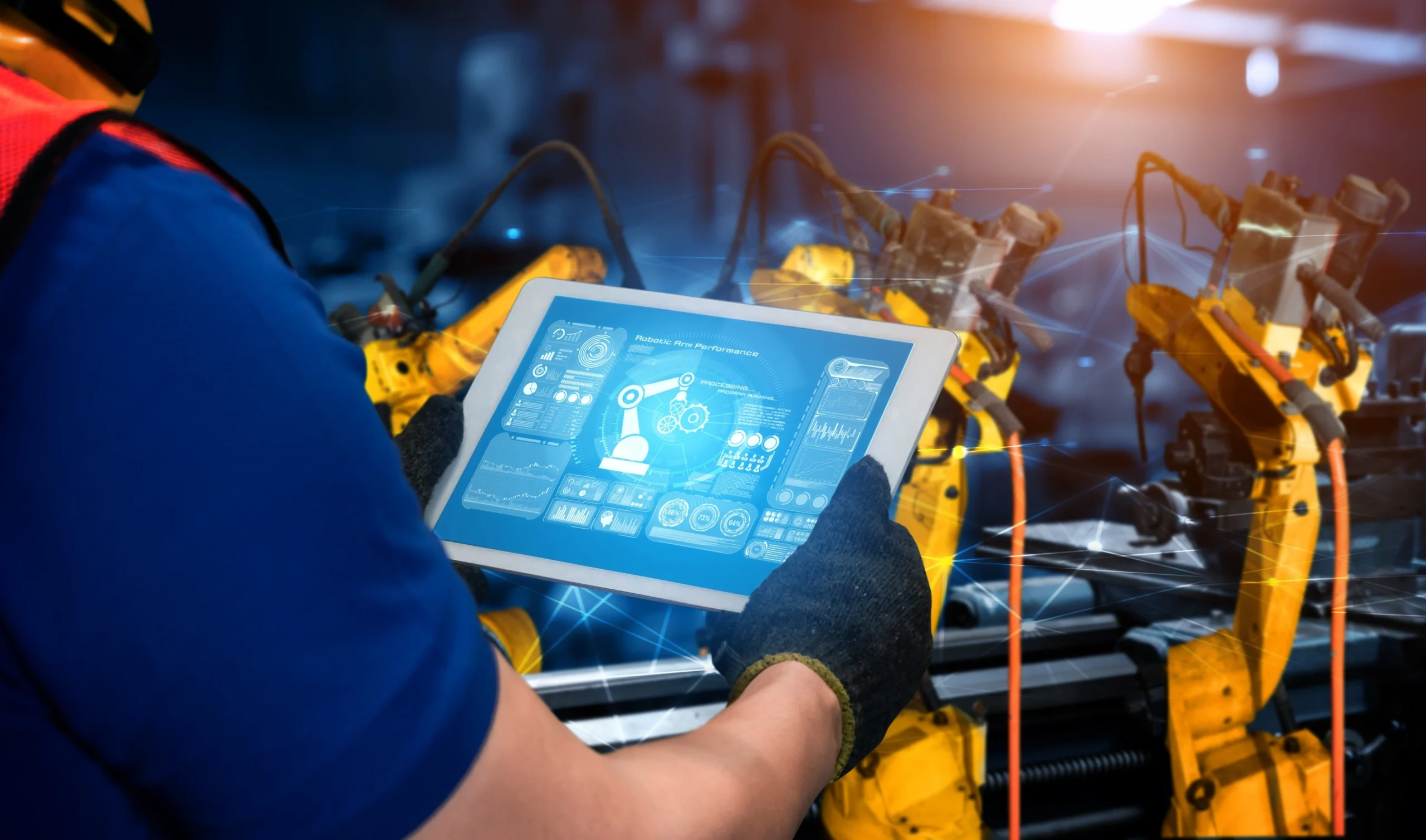
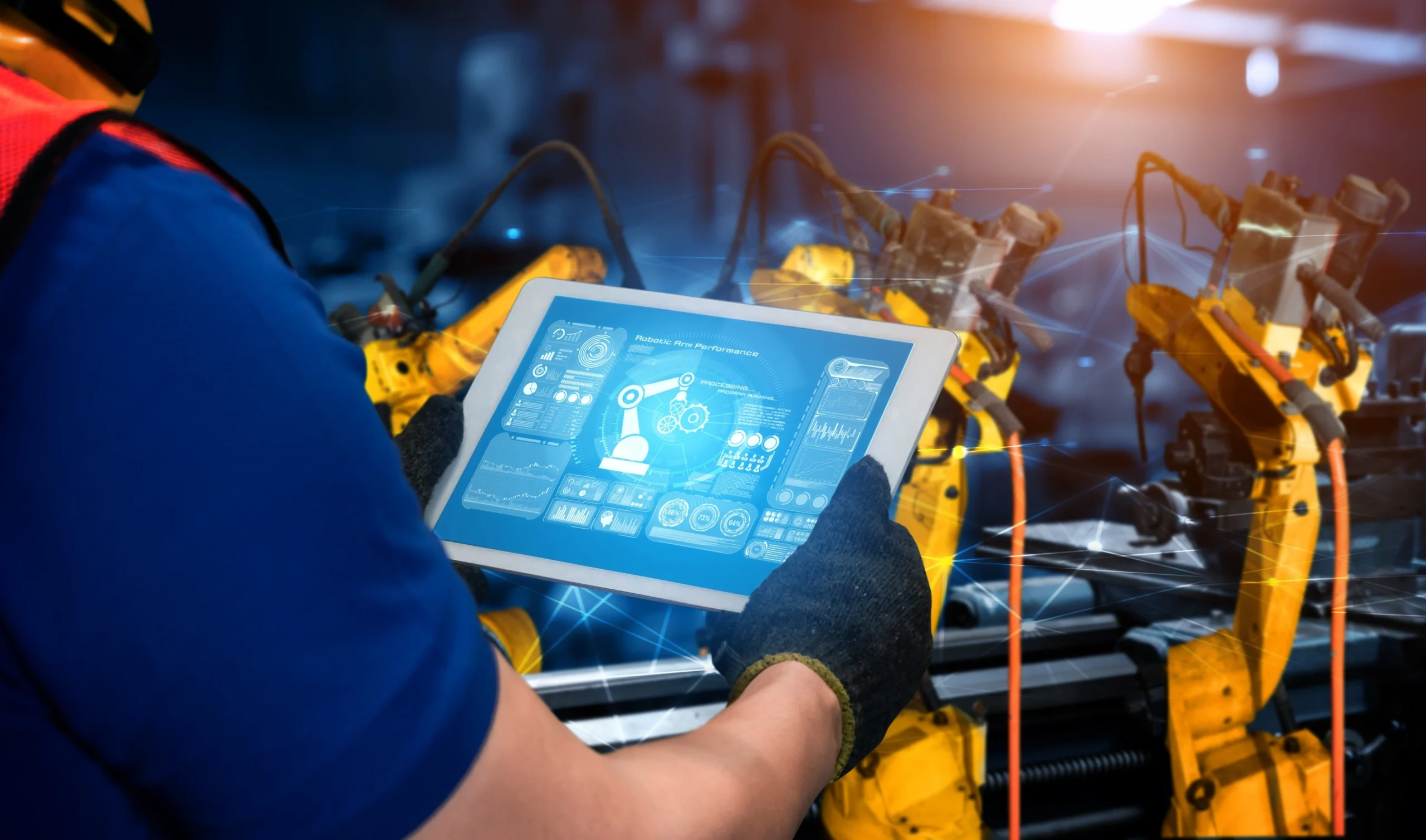
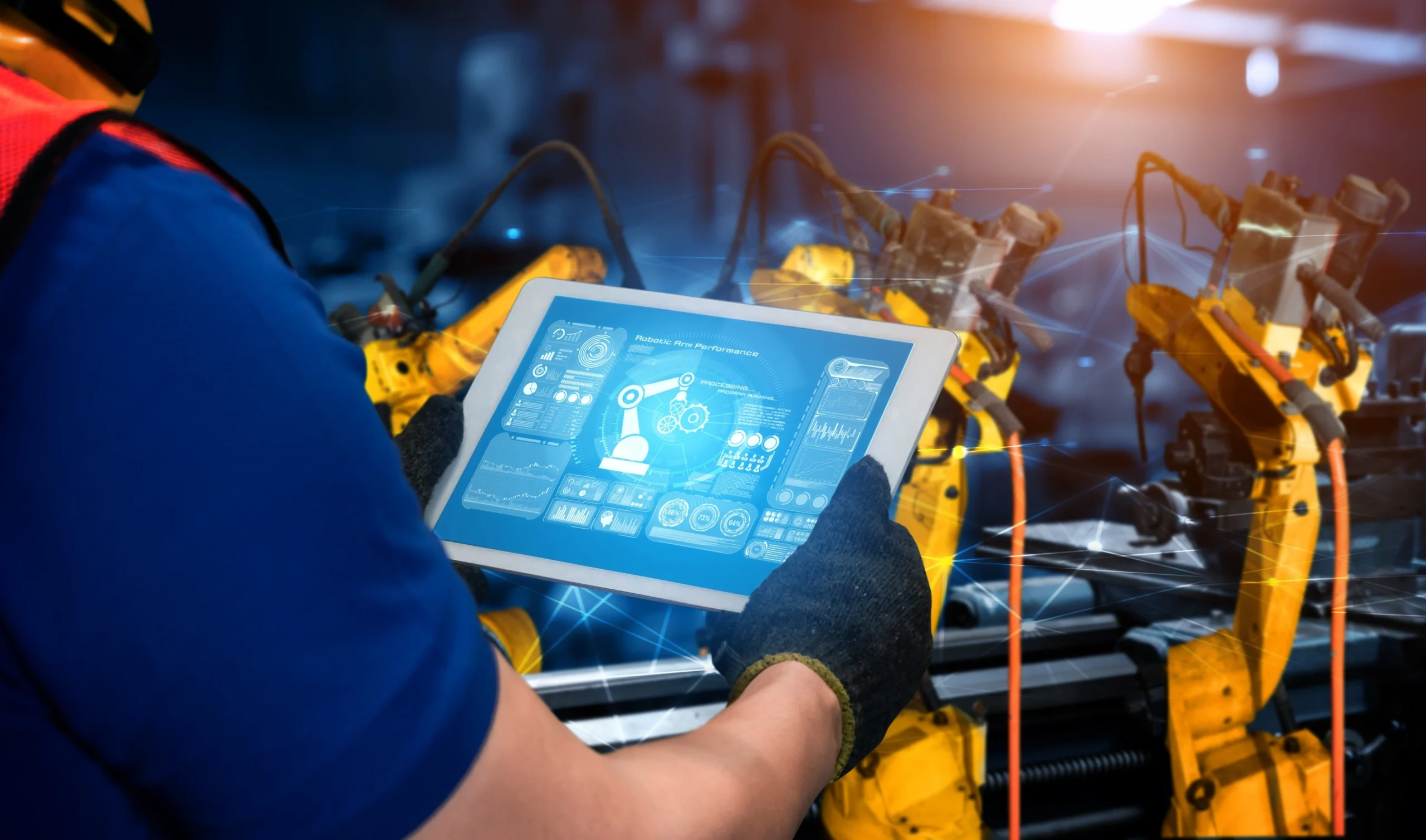
Predictive Maintenance in Indian Industries: Reducing Downtime with IIoT Solutions
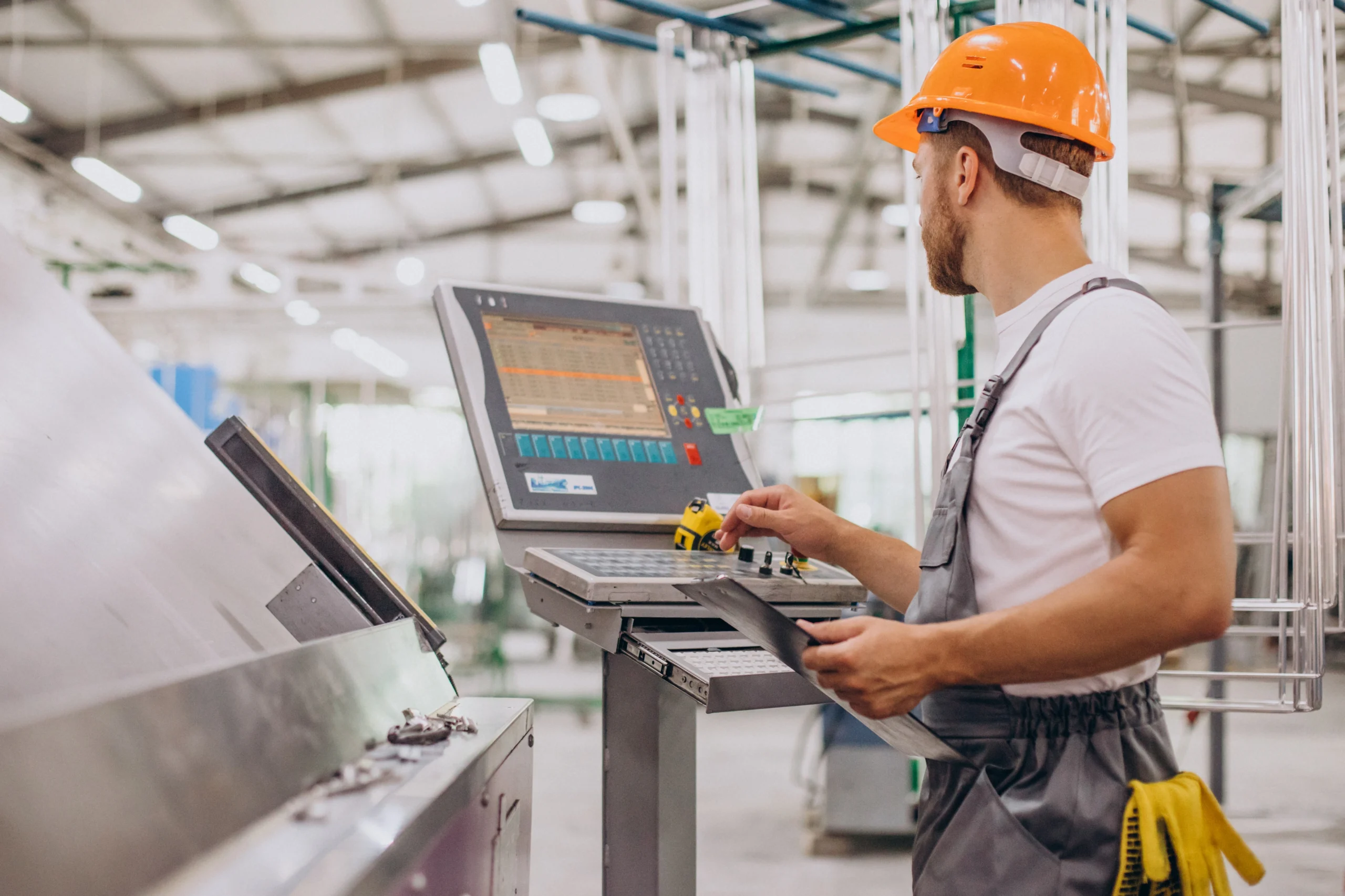
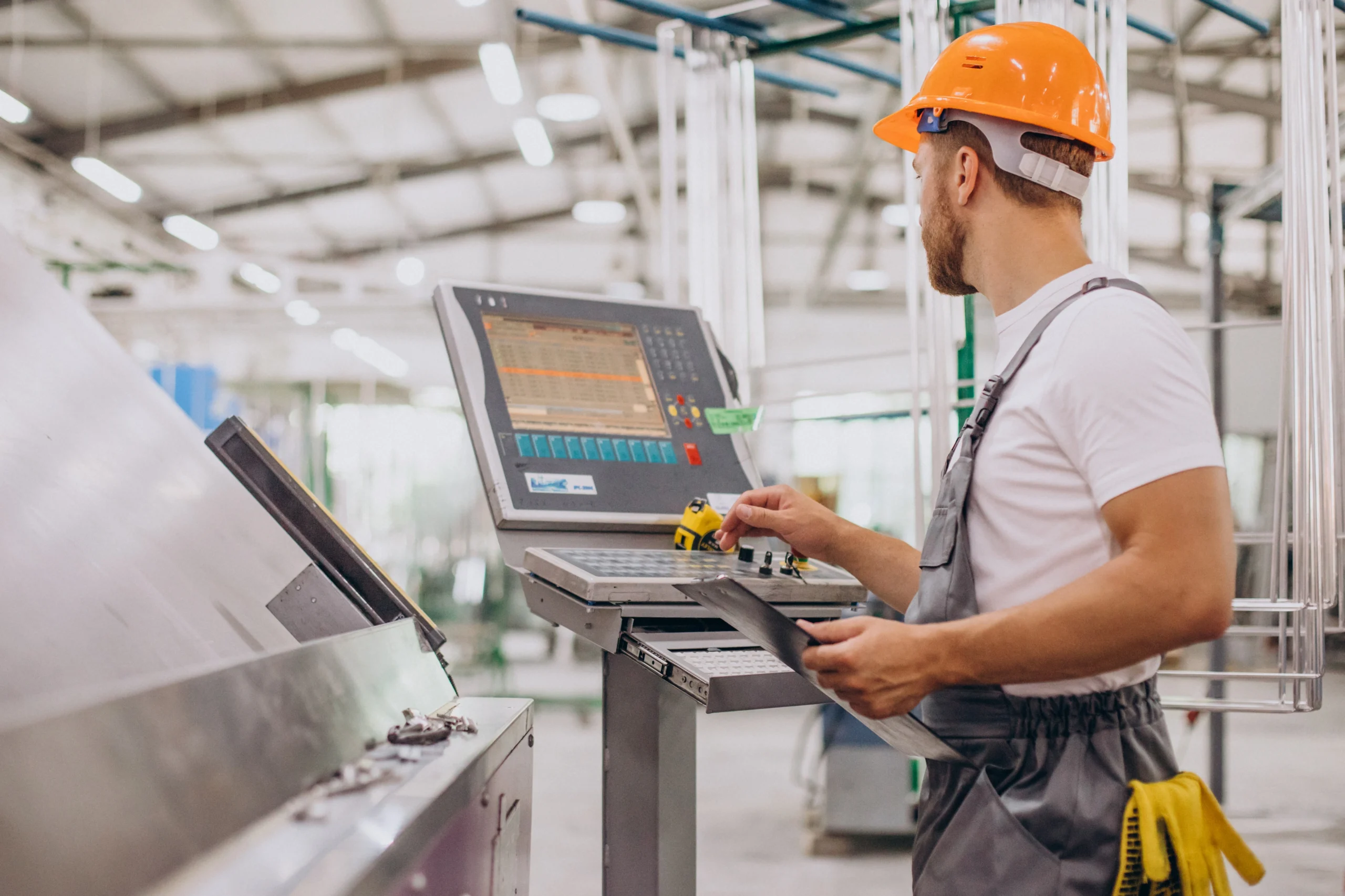
Maximizing OEE: How Real-Time Monitoring Transforms Manufacturing Efficiency
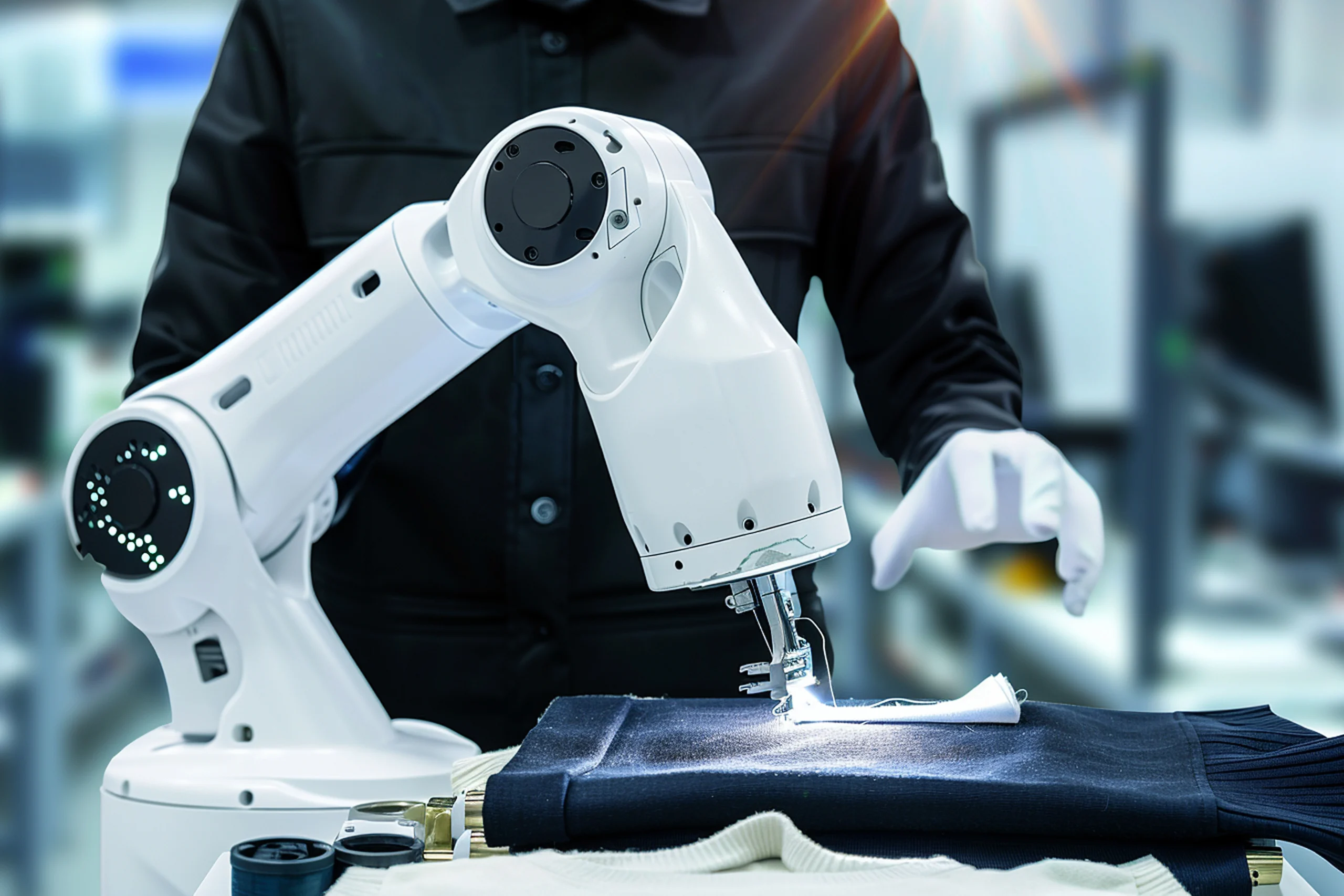
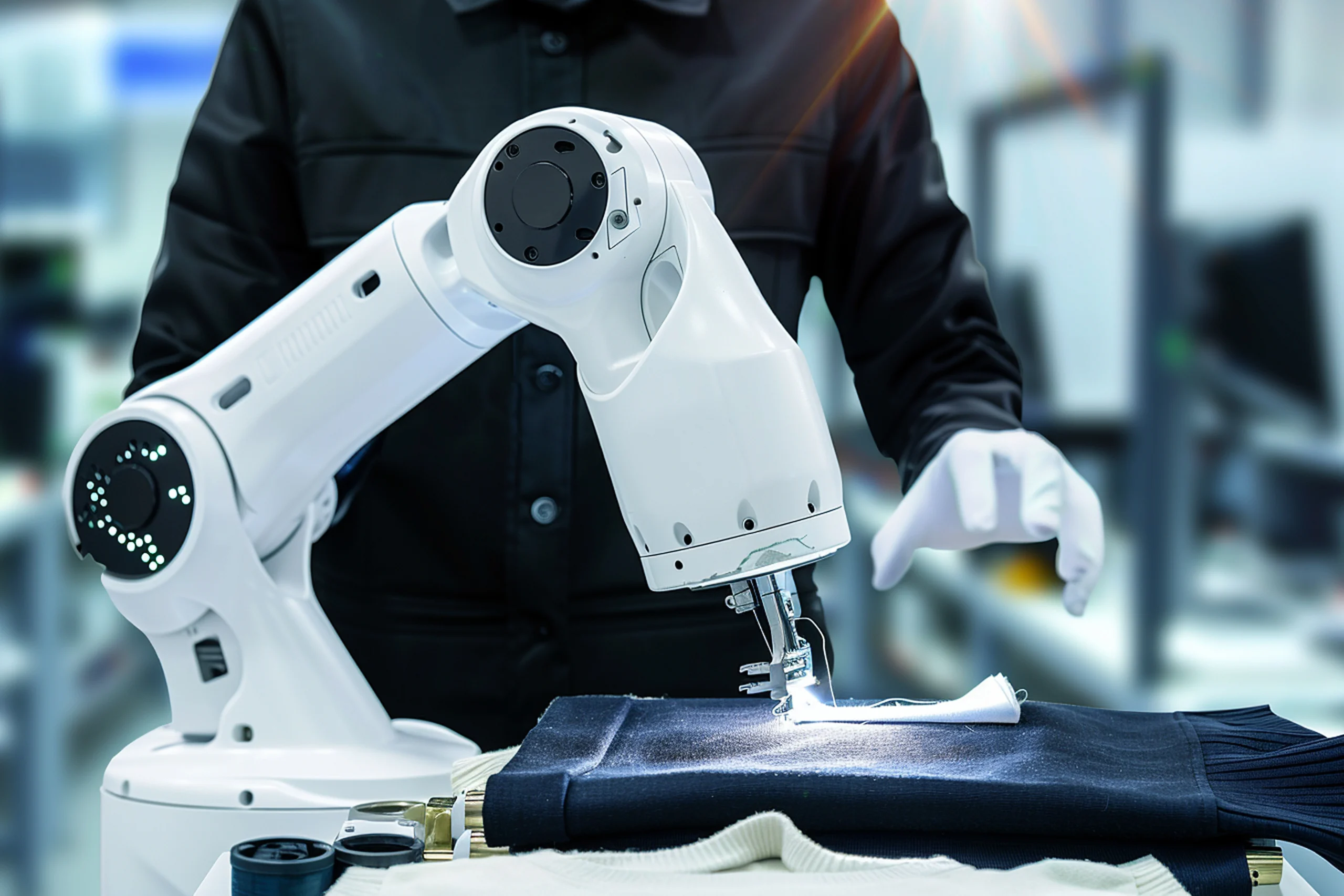
Smart Automation for Textile Machines with LXM28, LXM32, & Modicon M241
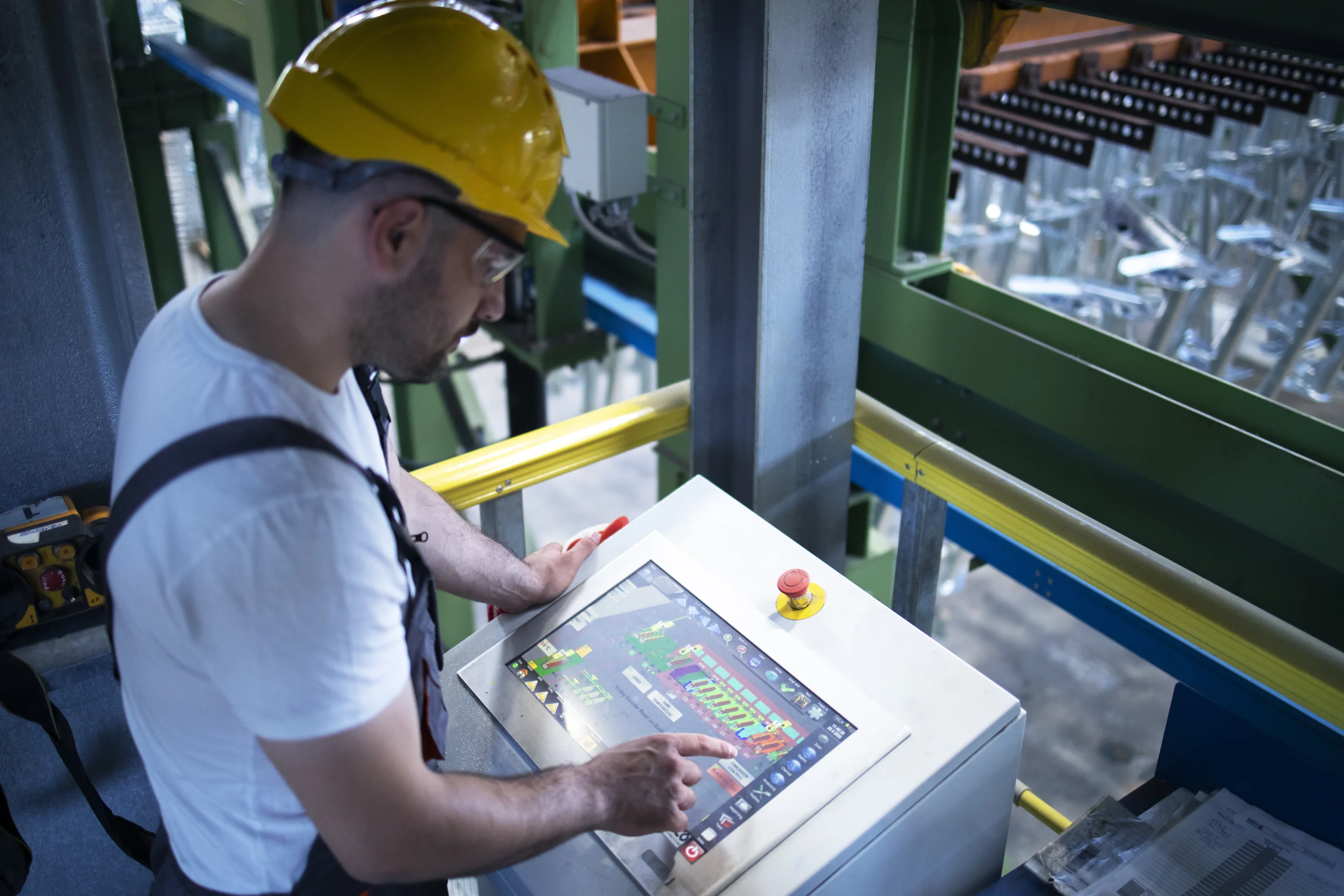
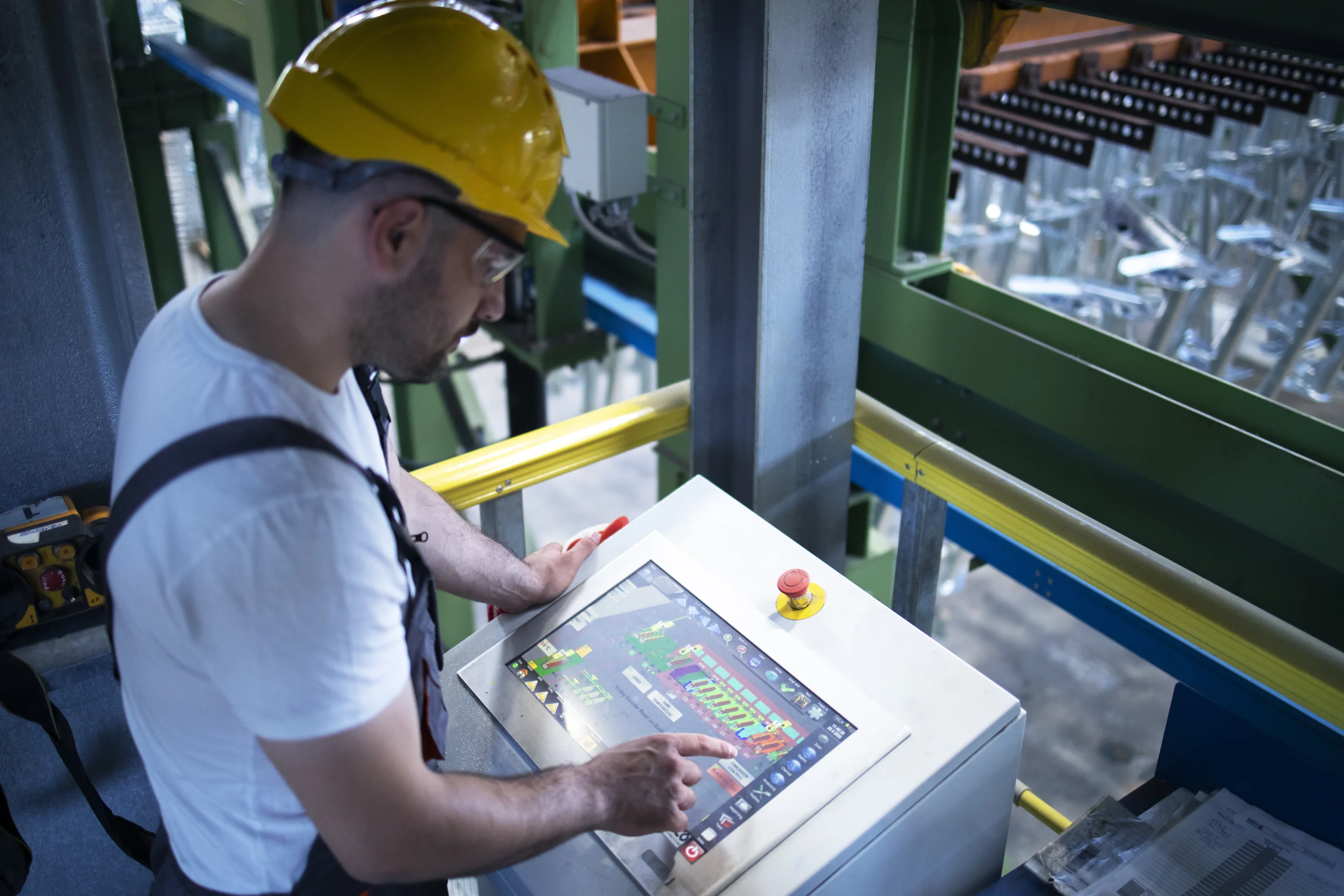
Complete Boiler Automation Using ATS Soft Starters and Modicon Controllers by Pima Contro
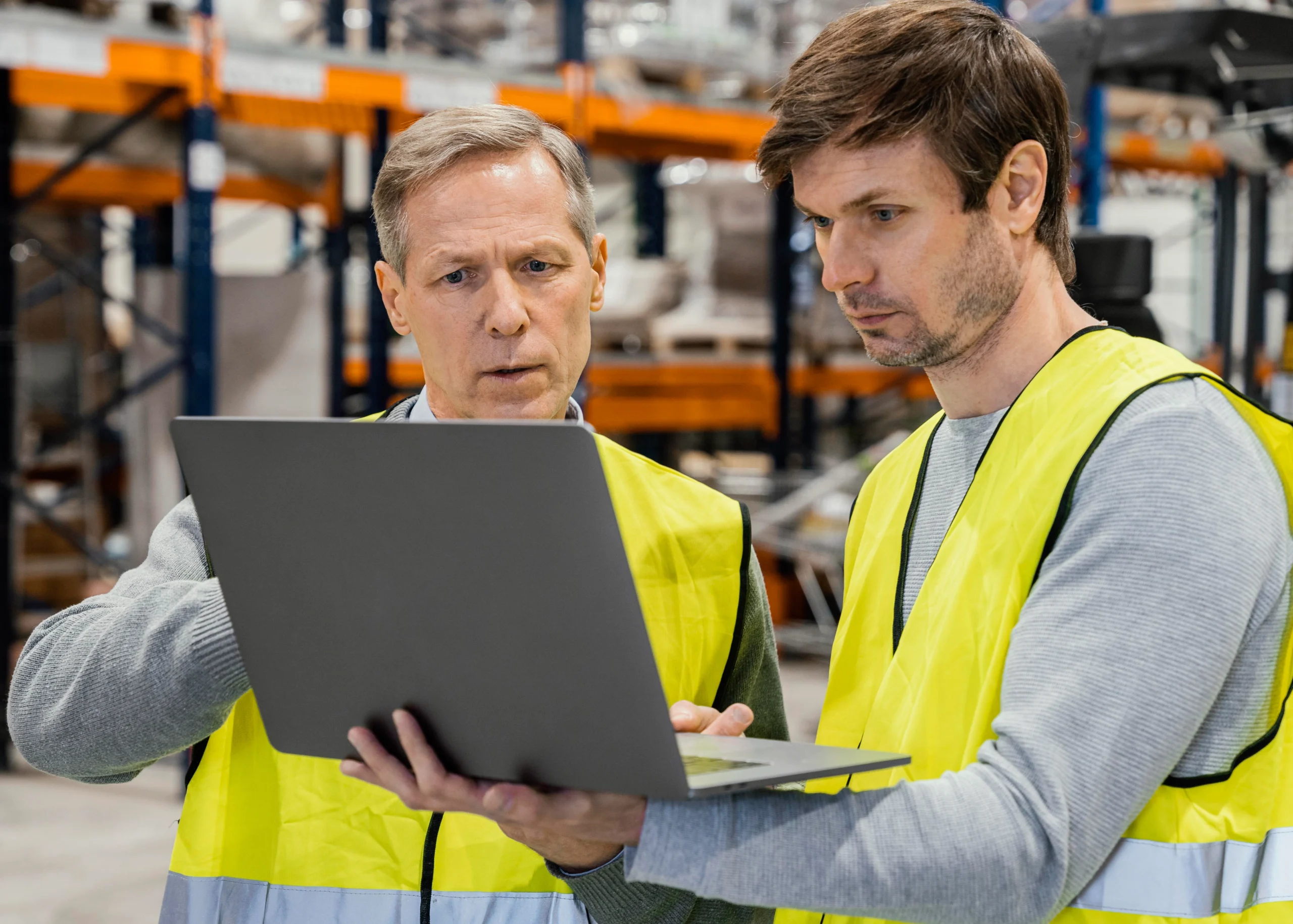
Smart Alerts in IIoT: Proactive Maintenance for Seamless Operations
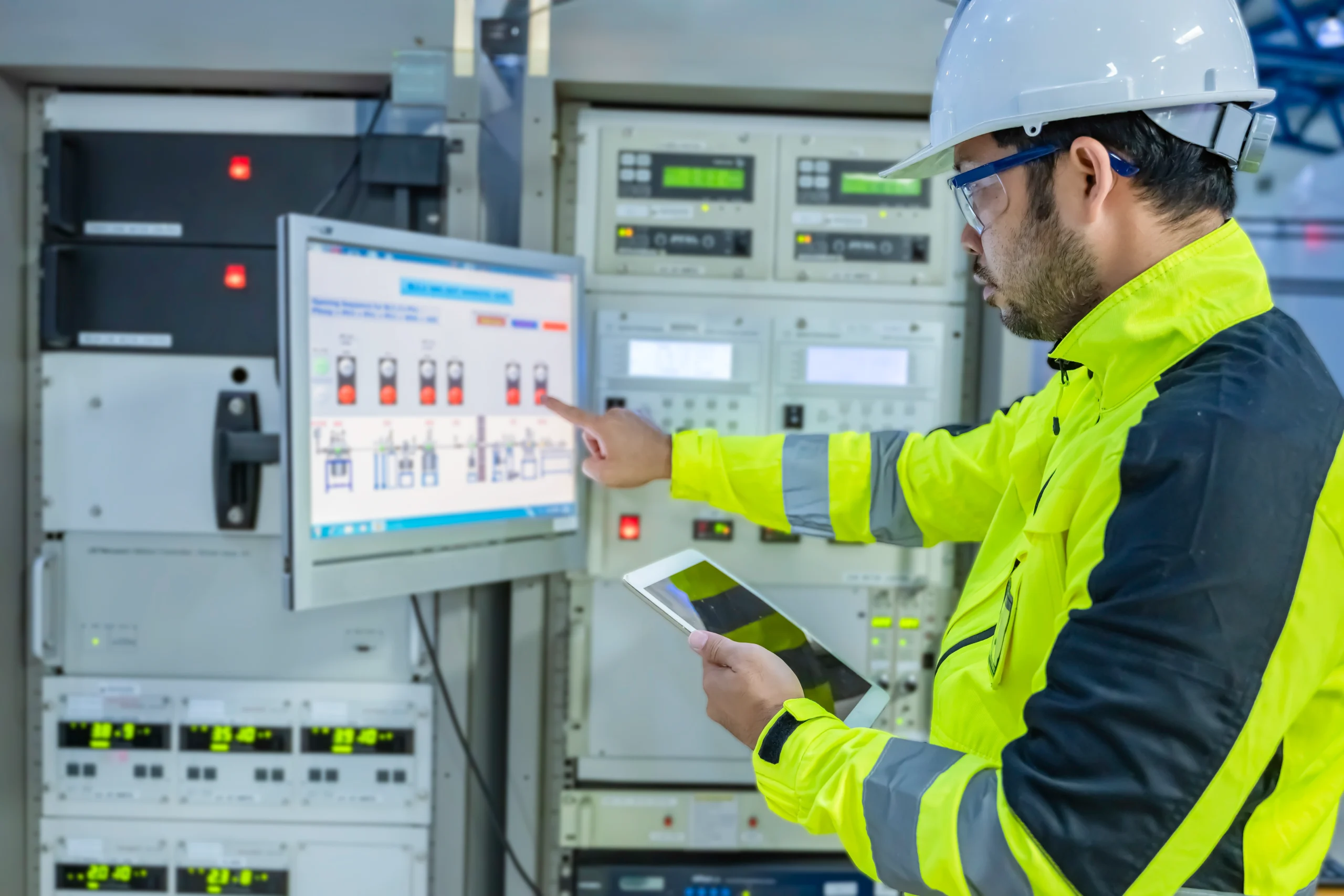
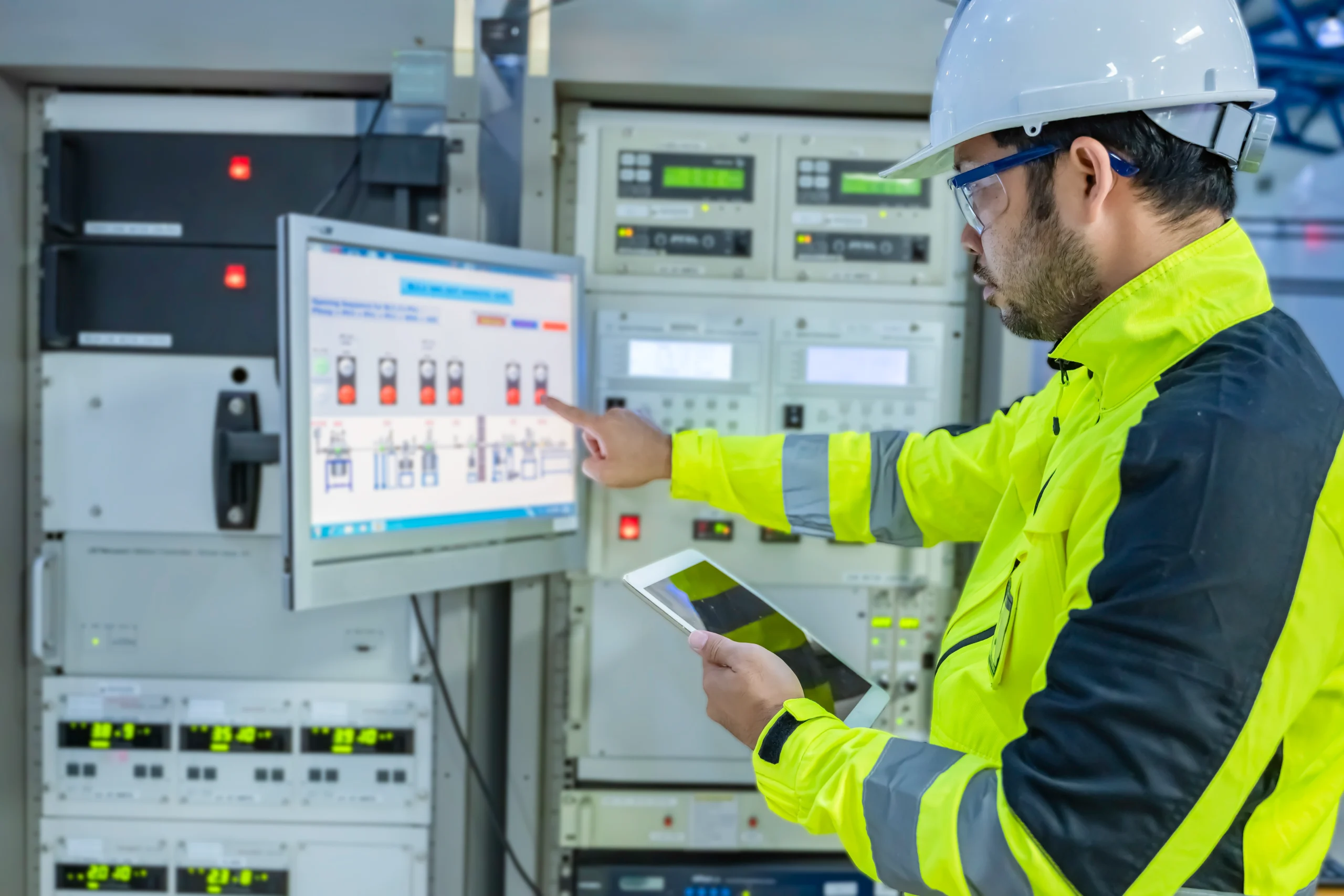
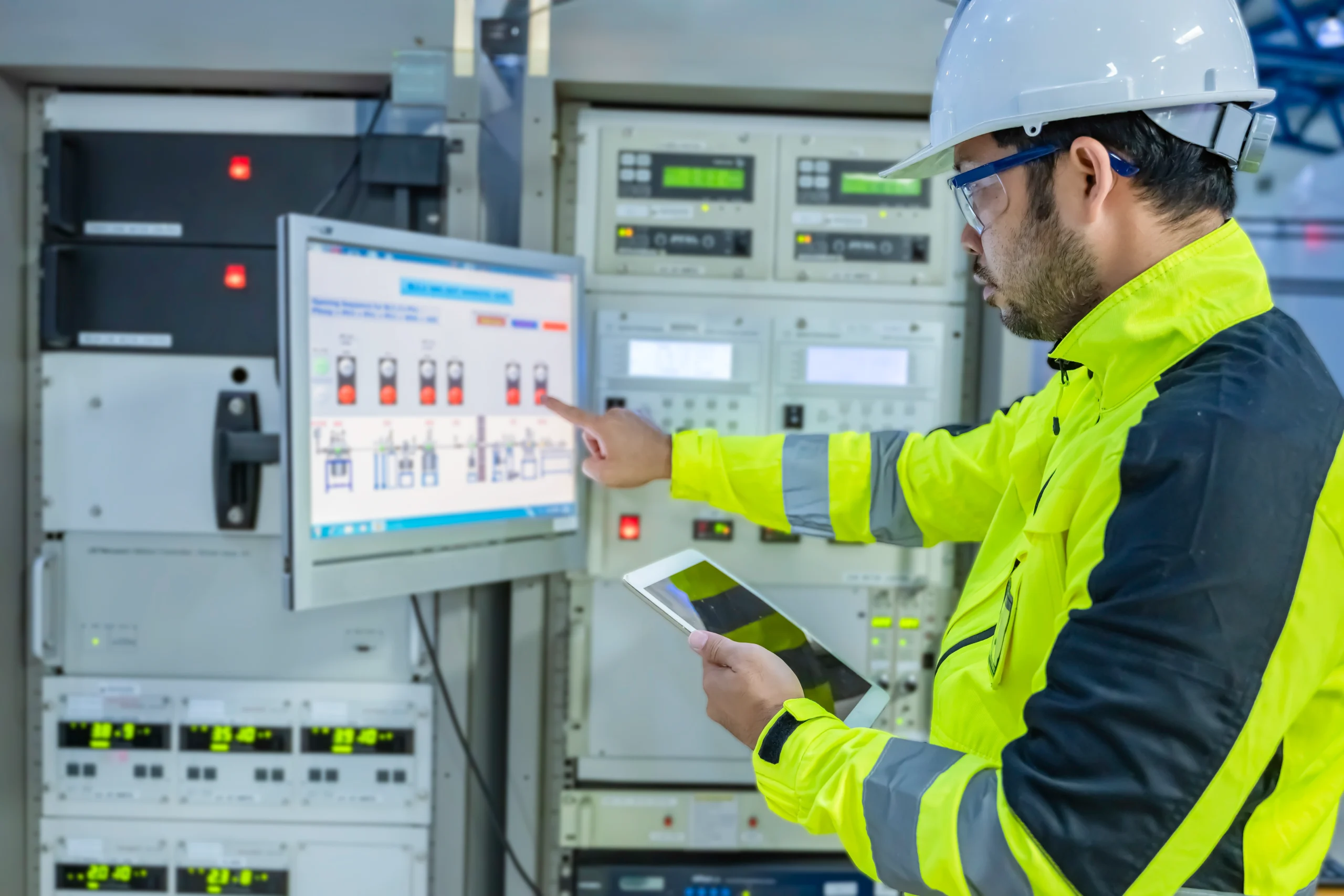
Energy Efficiency in Manufacturing: Leveraging IIoT for Cost Savings
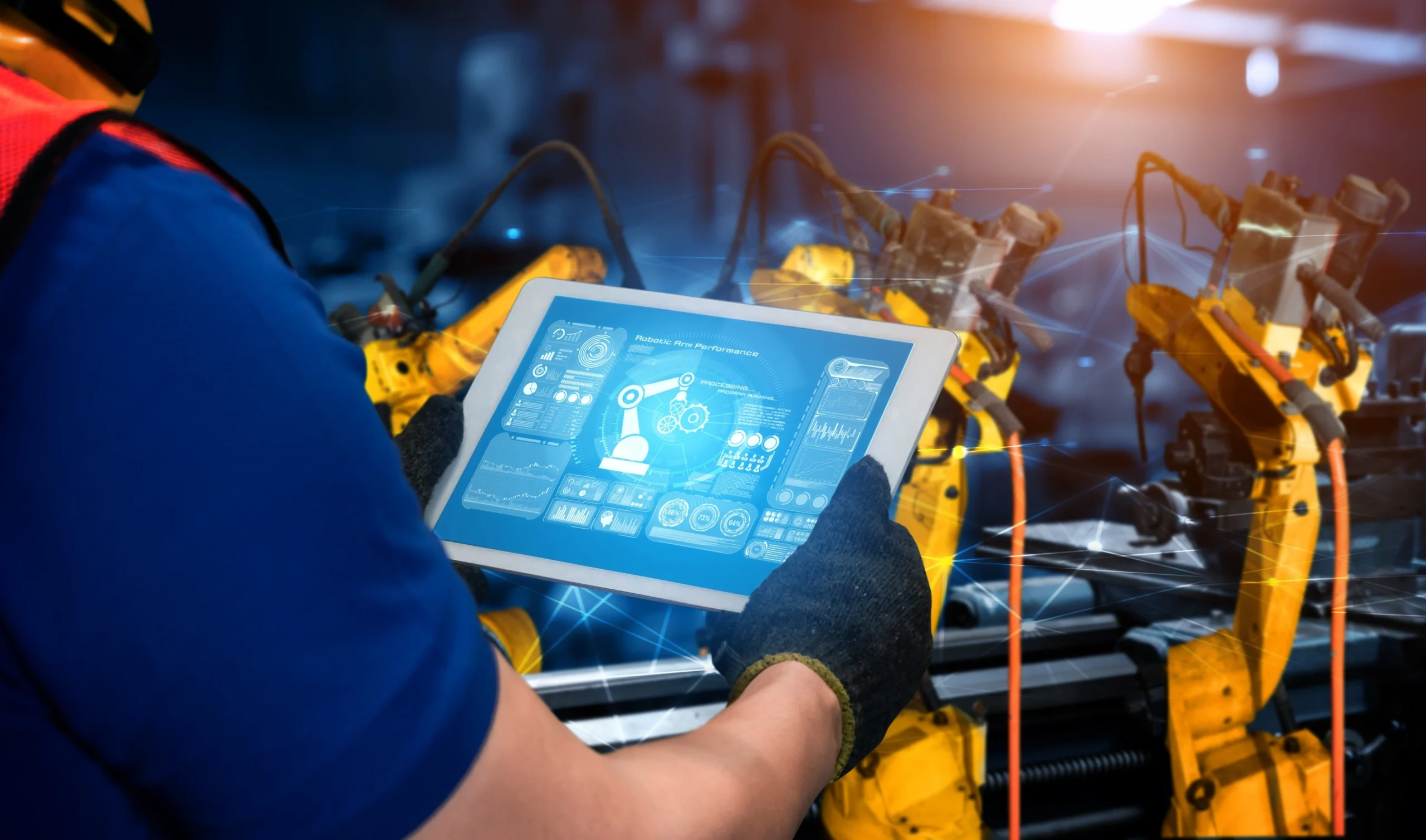
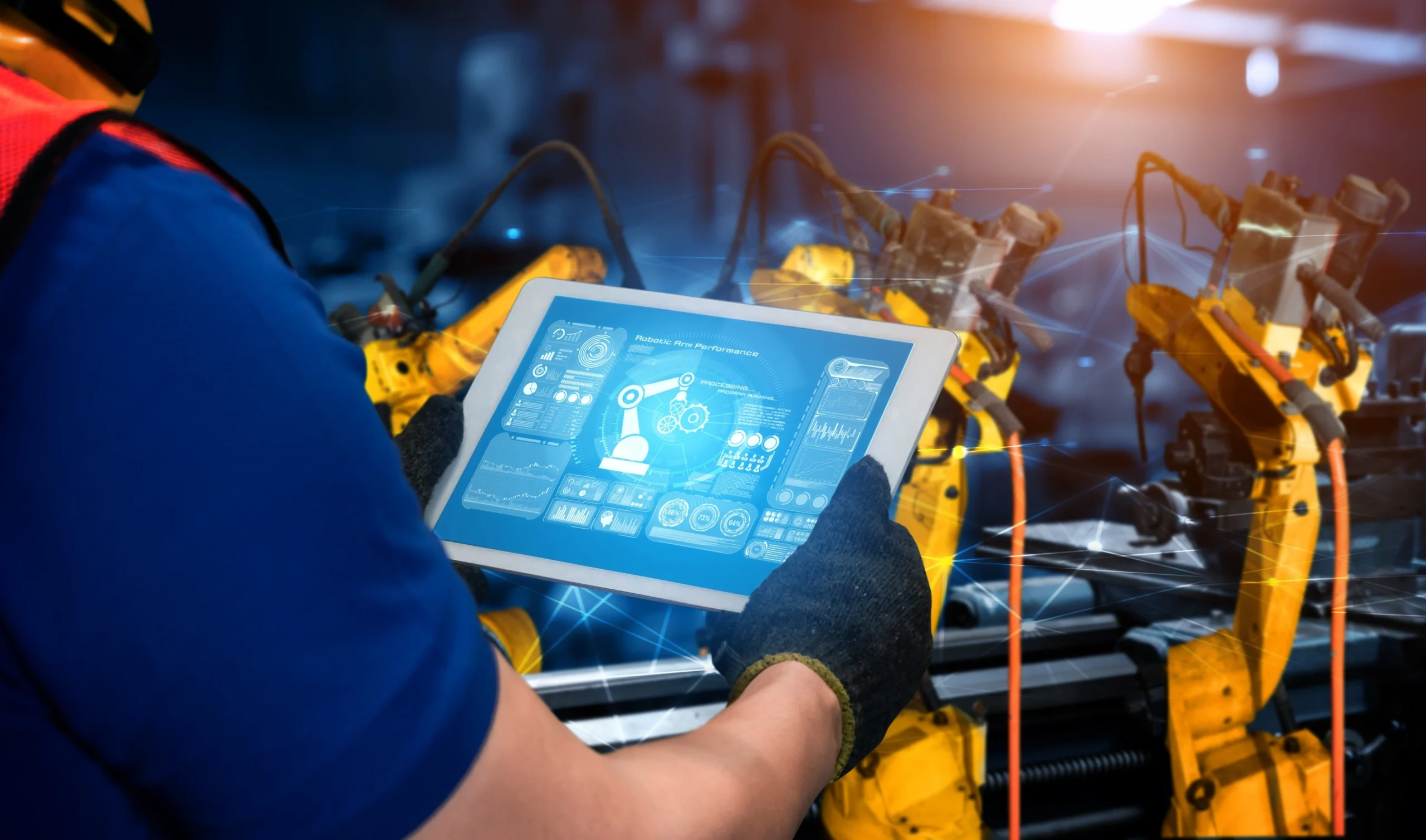
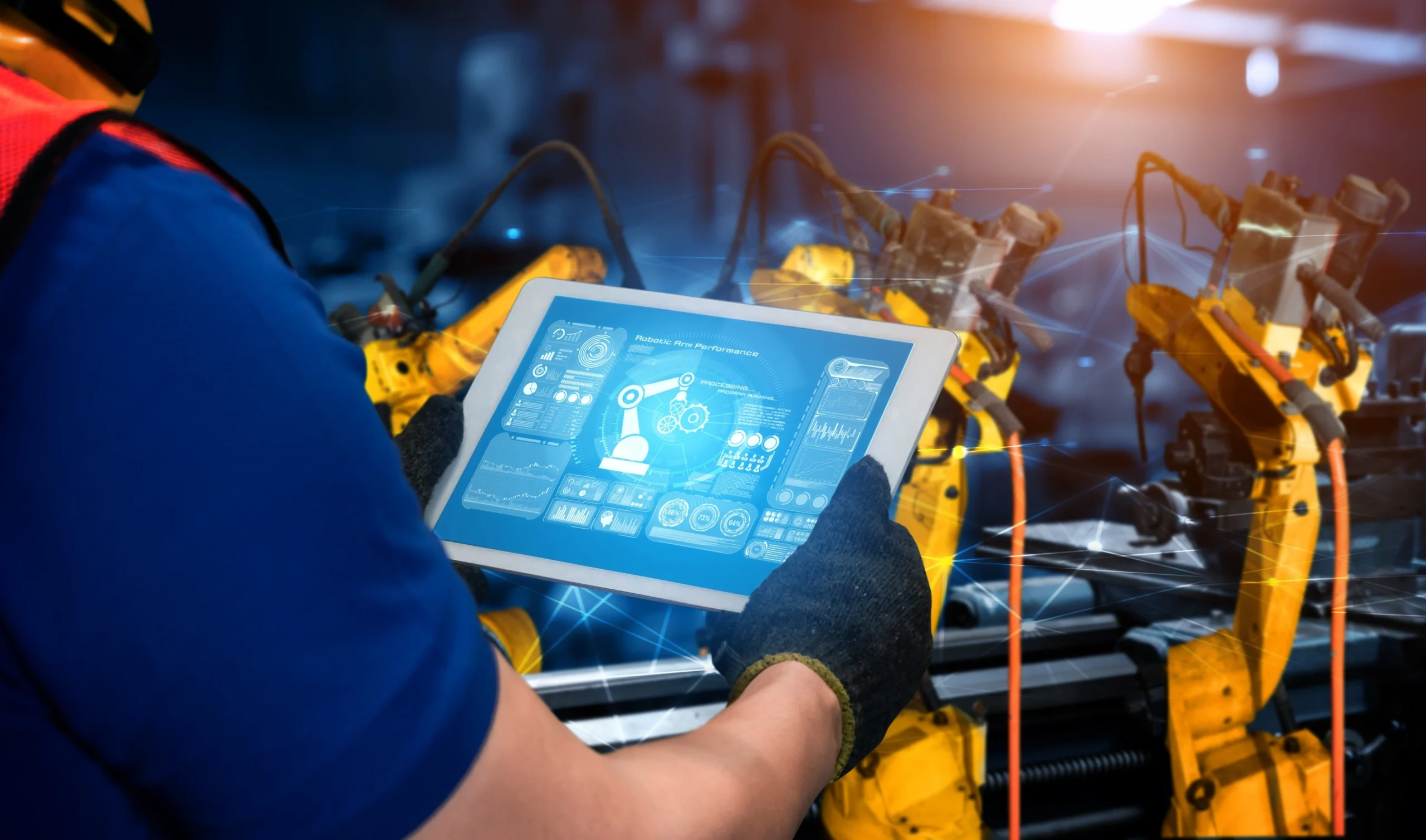